Das Bild zeigt eine Zusammenstellung verschiedener KarosserieBauteile von GF Casting Solutions für unterschiedliche Hersteller.
Die Zukunft ist gross
Fahrzeugkarosserien wurden bisher aus vielen Einzelteilen montiert. In Zukunft besteht eine Karosserie aus weniger und grösseren Leichtbau-Strukturteilen. Das reduziert Gewicht und steigert die Effizienz in der Produktion – auch bei GF Casting Solutions.
Kaum eine Branche verändert sich derzeit so stark wie die Automobilindustrie. Das betrifft vor allem die Fahrzeugelektronik. Volkswagen beispielsweise kommt derzeit noch mit 10 bis 100 Millionen Codezeilen in der Software seiner Autos aus. Bald dürften es jedoch schon 200 bis 300 Millionen Codezeilen sein, rechnet das Unternehmen laut Medienberichten.
Welchen Nutzen hat Big Casting?
Während IT-Systeme und Elektronik immer vielschichtiger werden, verringert Big Casting bei der FahrzeugKarosserie die Komplexität auf der Kundenseite. Statt vieler Einzelteile aus Blech oder Extrusion produzieren Druckgussmaschinen beispielsweise einen partiellen Vorderwagen oder eine Heckstruktur auf einmal. Weniger Einzelteile und Arbeitsschritte haben viele Vorteile: Sinkende Fehleranfälligkeit und weniger Verschnitt sparen Geld und Energie. Die grösseren Bauteile sind passgenau und spezialisiert auf das jeweilige Fahrzeugmodell und auf Kundenwünsche zugeschnitten.
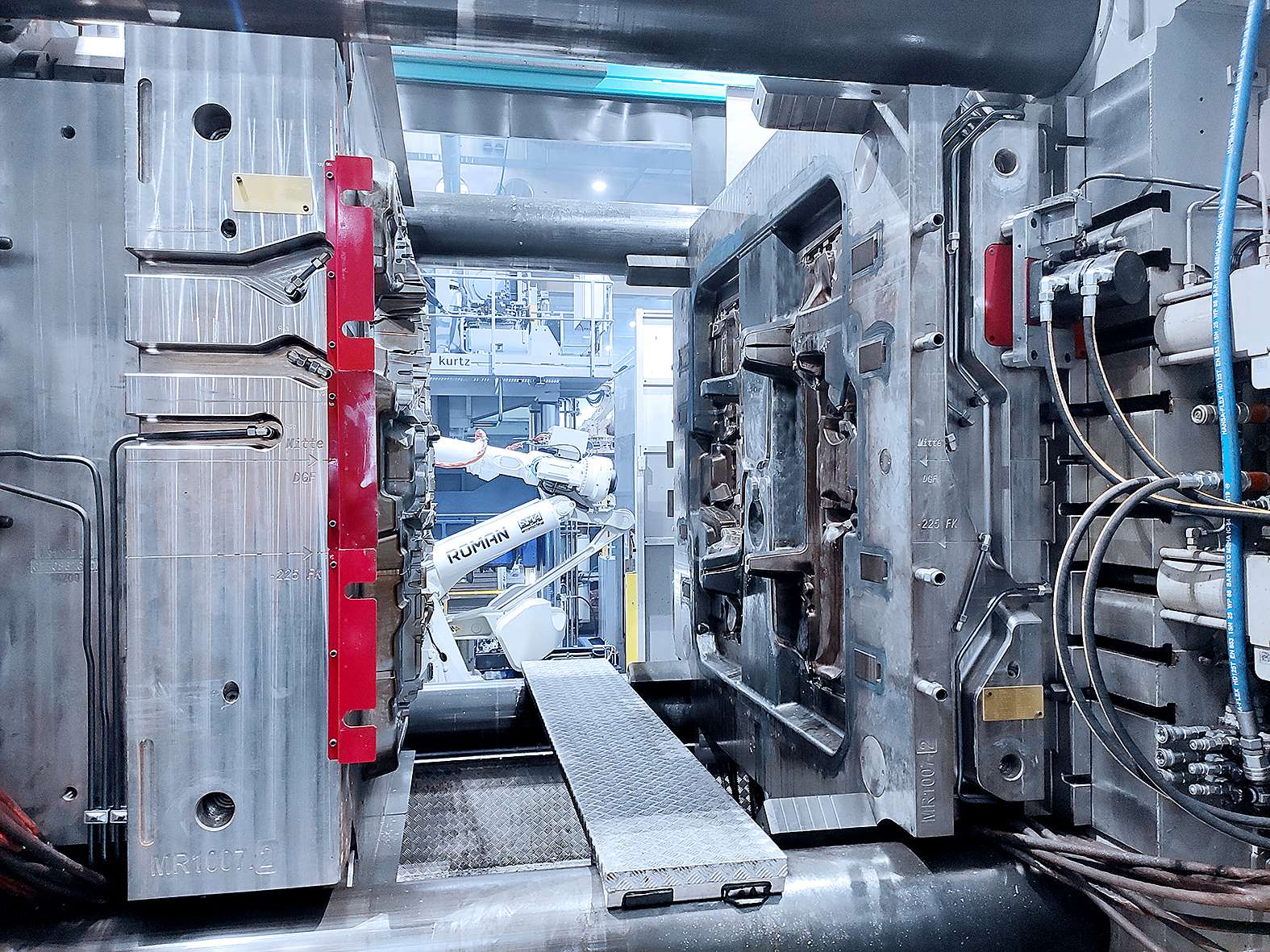
GF Casting Solutions arbeitet in verschiedenen Entwicklungsprojekten daran, mehrere Einzelbauteile zu einem grossen Bauteil zu integrieren. Damit wird automatisch auch die Quantität der erforderlichen Einzelwerkzeuge und die Komplexität der Verbindungstechnik wie Schweissen reduziert. „Wir haben ein grosses Druckgusswerkzeug und dort wird das Bauteil mit nur einem Schuss hergestellt. Wir setzen Big Casting gemäss unserer Strategie 2025 konsequent um. Wo immer möglich entwickeln wir die Bauteile so, dass sie mit grossen Druckgussmaschinen mit 4’400 Tonnen hergestellt werden können“, sagt Frank Gensty, Chief Technology Officer (CTO) bei GF Casting Solutions. Fügeprozesse zum Verbinden von Teilen und Montageschritte beim Kunden werden dadurch erheblich optimiert.
Produktionszeit halbiert
Ein weiterer Vorteil von Big Casting ist die Zeiteinsparung: „Wenn die Fahrzeughersteller einen kompletten Vorder- oder Heckwagen montieren, können sie die Produktionszeit eines Fahrzeugs stark reduzieren“, sagt Frank. Ein typisches Mittelklasse-Fahrzeug wird dadurch statt in 25 Stunden in nur 10 Stunden produziert. Die Produktion grösserer Teile und deren Einbau verlangen auch entsprechende Anpassungen der Anlagentechnik auf der Kundenseite. Viele Kunden haben laut Frank bereits eine maximale Obergrenze für die zu verwendenden Druckgussmaschinen getroffen, um eine bestmögliche Effizienz der bereits vorhanden Analgentechnik zu erreichen. Gleichermassen bedeutet dies auch Anpassungen auf der Logistikseite, wenn es beispielsweise um den Transport und die Lagerung der grösseren Teile geht. Auch die Maschinen, die die Big Castings herstellen, werden natürlich grösser und schwerer. Dieses wiederum hat direkten Einfluss auf die Infrastruktur eines Werks.
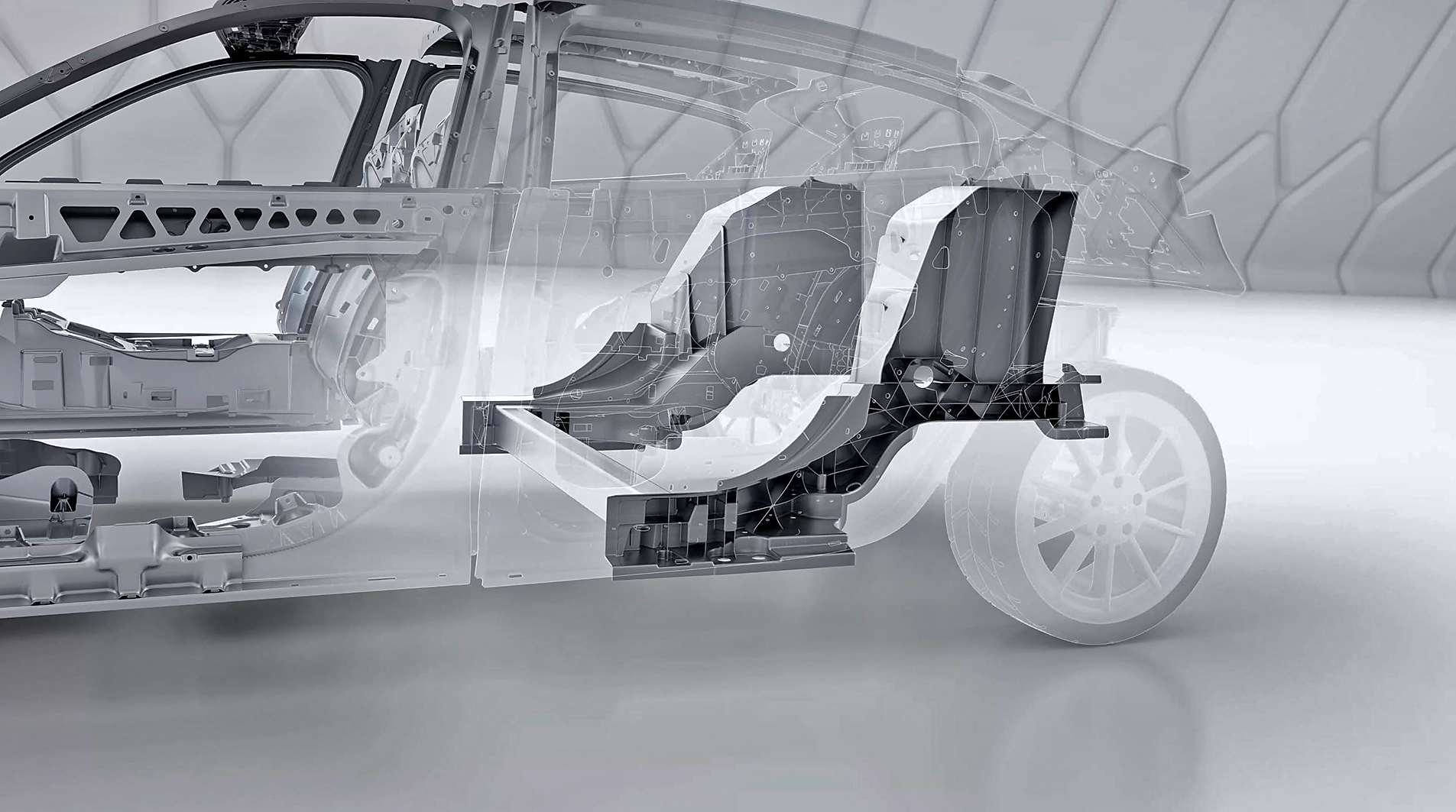
Nachhaltigkeit ist der Antrieb
Für mehr Nachhaltigkeit entwickelt GF Casting Solutions den sogenannten CO2-Calculator, um genaue Angaben über die Nachhaltigkeit der Produktion machen zu können. Frank erklärt: „Jeder Kunde von uns wird eine explizite Aussage über den CO2-Fussabdruck des bei GF produzierten Gussteils erhalten. Der Vorteil ist, dass wir damit auch Bauteile in der Entwicklungsphase entsprechend vorsimulieren können.“ Obwohl der Trend Big Casting in der Fahrzeugbranche noch recht neu ist, gestaltet GF ihn bereits aktiv mit. „Wir sind mitten in der Umsetzung und entwickeln für unsere Kunden die jeweils ideale Lösung aus Leichtbau, Funktionsintegration, Performance, Wirtschaftlichkeit und ökologischen Aspekten“, so Frank. Nach Aussage des CTO setzen in Europa drei grosse Fahrzeughersteller auf Big Casting. „Es gibt einige Unternehmen, die ihre Strategie noch nicht final kommuniziert haben. Ausserdem werden traditionelle Fahrzeughersteller die technische Grenze einer 4’400-Tonnen-Maschine maximal ausnutzen“, analysiert Frank die aktuelle Situation in dem wachsenden Markt.
Klein, kompakt, leistungsstark
Lithium-Ionen-Batterien haben im Vergleich zu anderen Technologien die höchste Energiedichte: Sie können pro Kilogramm Batterie am meisten Energie speichern. Das macht sie zum Spitzenreiter für den Einsatz im E-Auto.
Damit die Produktion so lokal wie möglich erfolgen kann, betreibt GF je drei Druckguss-Standorte in Europa und Asien. Seit Kurzem kooperiert GF auch mit der auf Leichtbau-Gussteile spezialisierten Giessereigruppe Bocar Group mit Hauptsitz in Mexiko, um auch den US-Markt bedienen zu können. „Wir hören niemals auf, besser zu werden. Wachstum durch Innovation ist Teil unserer DNA bei GF“, ist Frank Gensty überzeugt.
Das steckt hinter Big Casting
Der Begriff Big Casting beschreibt die Herstellung besonders grosser Strukturgussteile für die Fahrzeugkarosserie.
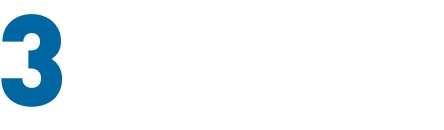
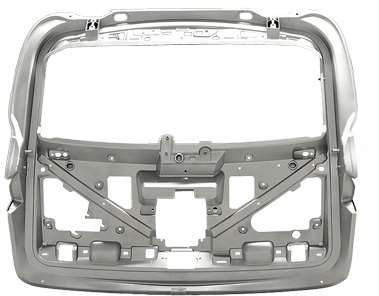
Besonderer Guss für E-Autos
Elektroautos benötigen im Bereich Antrieb andere Komponenten als Fahrzeuge mit Verbrennungsmotor, im Guss sind das beispielsweise Batteriegehäuse oder Elektromotorgehäuse. Leichte Strukturbauteile (Front End Carrier oder Rear Side Member) aus Magnesium und Aluminium machen das ganze Auto leichter.
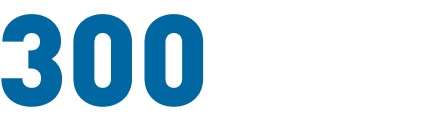