A smart start to the future
Examples from our divisions show how GF is intelligently implementing smart solutions to improve both in-house and customer processes.
Visitors to the new GF Machining Solutions Medical Solutions Center (Medical CoC – Center of Competence) in Schondorf (Germany), which opened in July 2021, may wonder at the first impression that they have entered a high-end automotive dealership. But instead of cars, the building houses different GF machines illuminated by spotlights and presented like luxury sports vehicles. These prize exhibits are used to manufacture medical technology products. “At this facility, we can explain the entire manufacturing process to customers and even produce prototypes right before their eyes,” says Benjamin Sendler, who regularly hosts managing directors, production specialists, and machine operators right here in the 1’200-square-meter showroom of the Medical CoC. With its innovative machines and software tools for the medical sector, the Medical CoC serves as an example of smart solutions at GF and an apt symbol for the GF Strategy 2025, which aims to achieve growth though intelligent, sustainable solutions. But in the case of the Medical CoC, the term “ intelligent” has more than one meaning. Customers benefit from both intelligent machines and the smart software that controls production processes and captures traceable production data. These innovations help visitors to the Medical CoC find the perfect solutions for their individual applications.
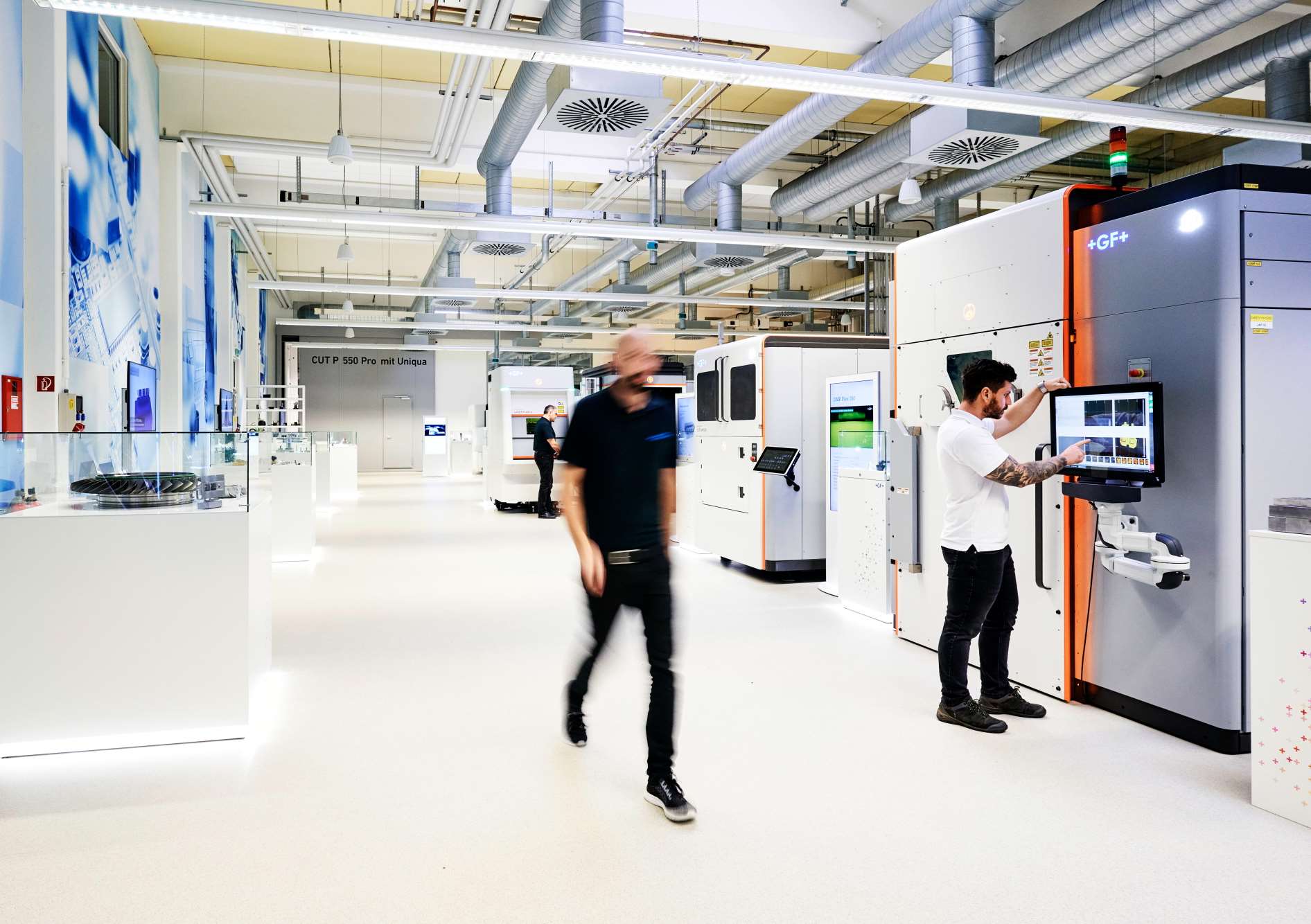
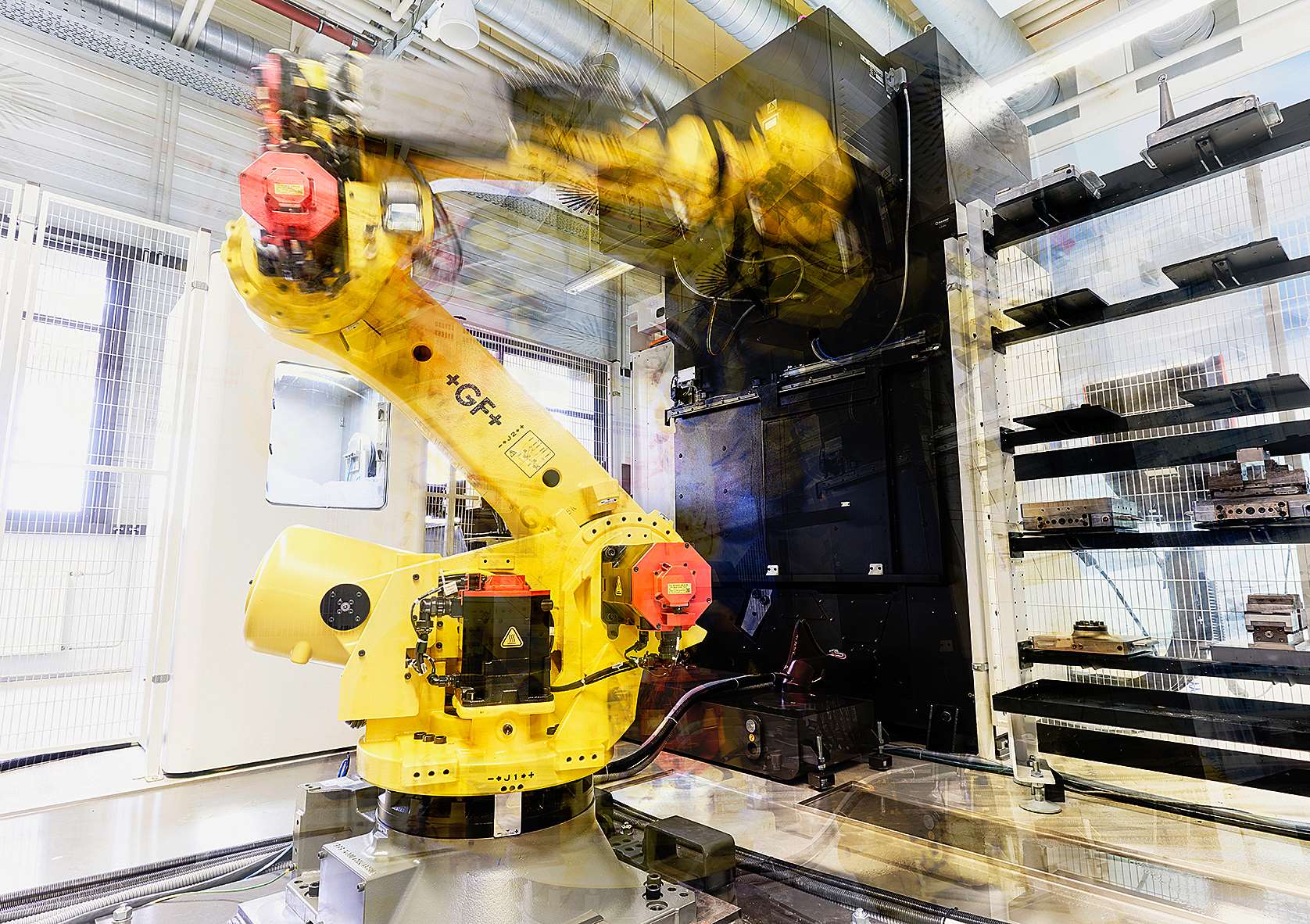
Experiencing manufacturing up close
Benjamin Sendler uses an example to illustrate how the process works in practice: In order to implant an artificial knee joint, the surgeon requires a surgical cutting block. This cutting block is placed on top of the shinbone (tibia) to mark the precise location where the surgeon must make the incision to remove the damaged knee joint. At the Medical CoC, customers can view the manufacturing process used to make these surgical aids up close and in person. The order is created in WorkShopManager, the GF software, after which the stainless steel blank proceeds through multiple high-precision manufacturing steps, including milling and laser texturing and finally, trimming the guide slot. “ After these three processing steps, we lay the finished component on the table in front of our guests. The data pertaining to the manufacturing process can be accessed via QR code,” explains Sendler. “In addition to the processing technologies for the cutting block, the Medical CoC also hosts other solutions, such as the additive manufacturing equipment for shoulder joint implants with porous surfaces. Many medical technology products can be produced start to finish using only GF machines, thanks to our extensive portfolio.”
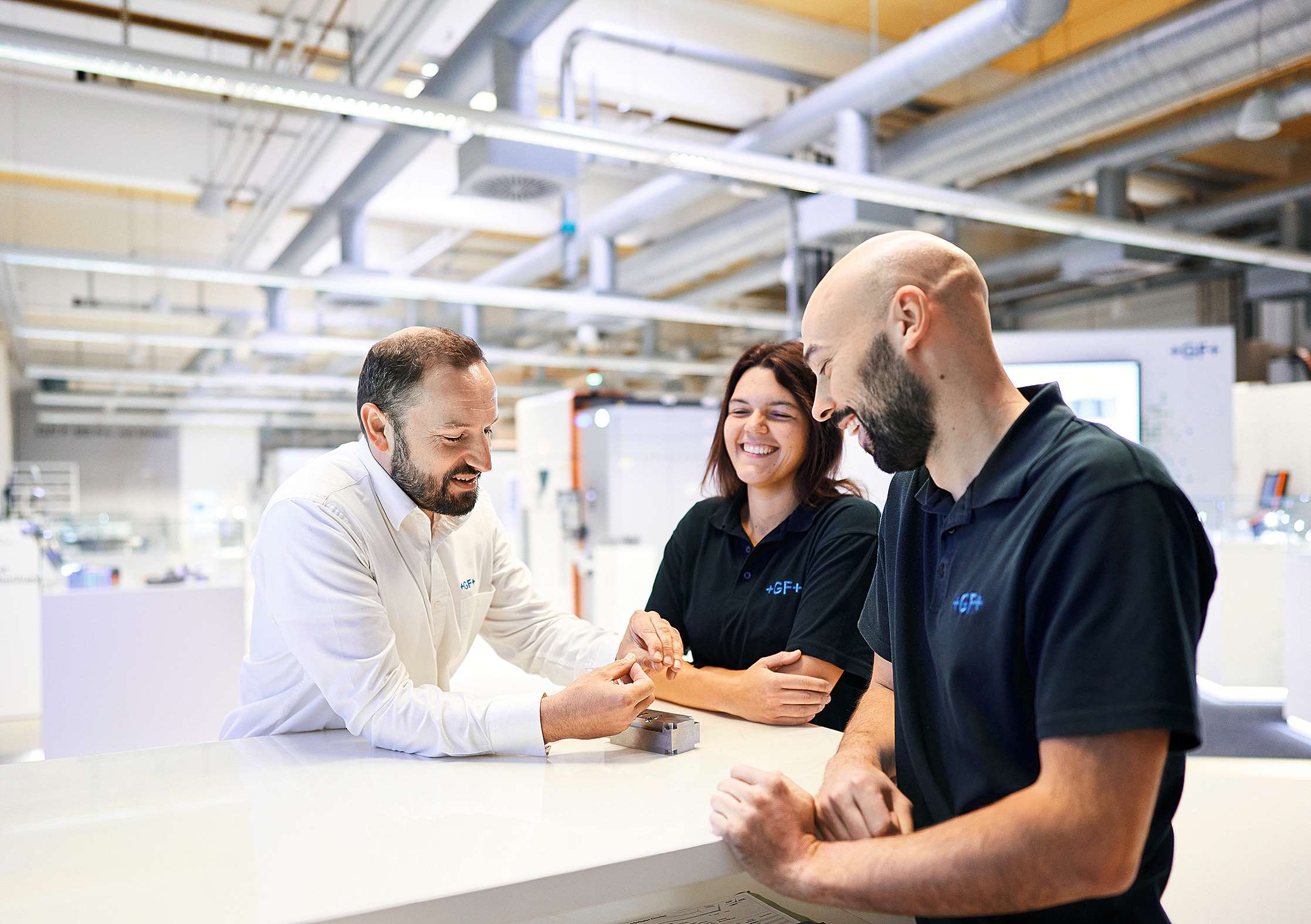
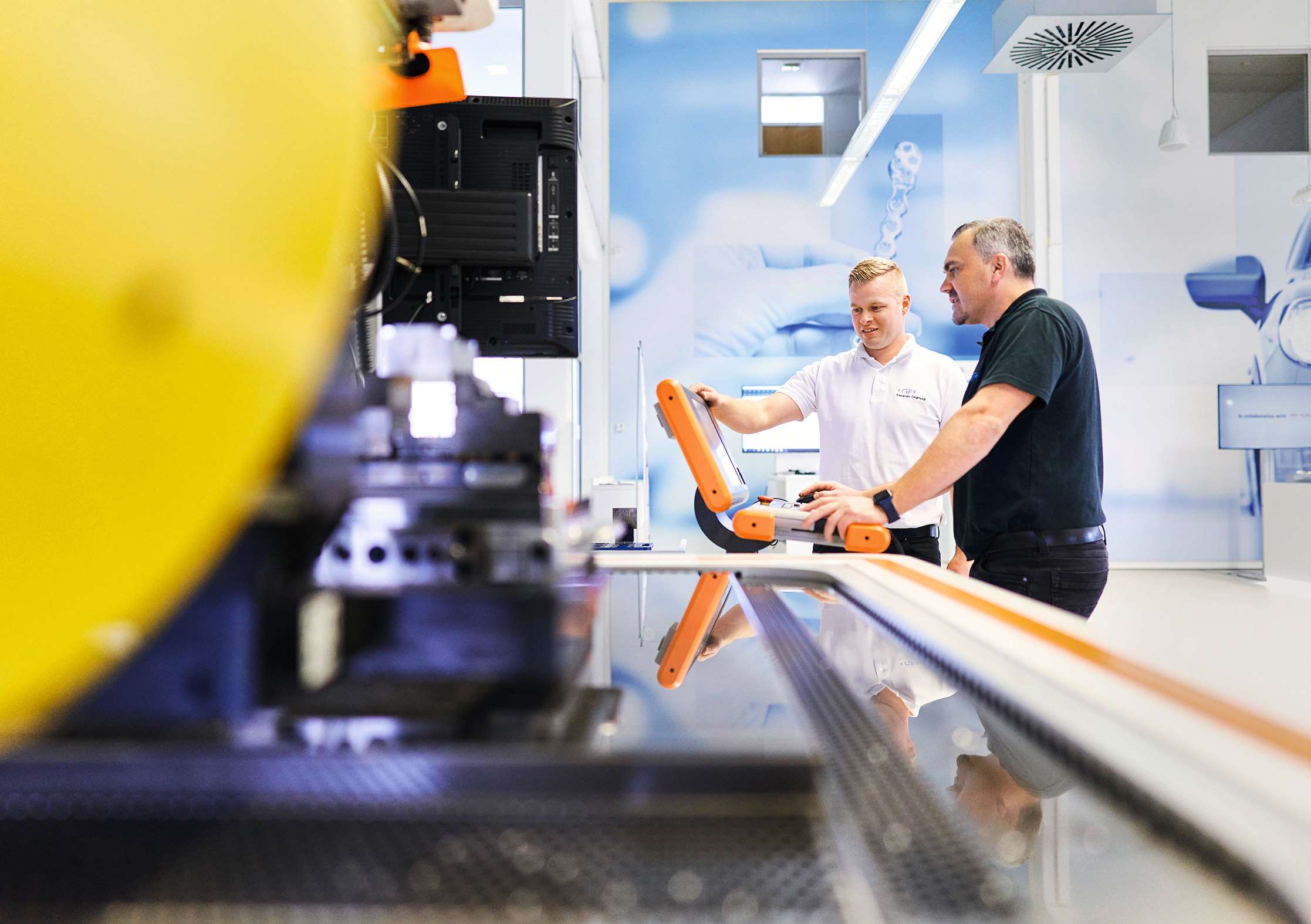
A new dimension of traceability
The strict laws governing the medical technology sector require maximum transparency. For certain products, manufacturers must be able to pinpoint exactly when the product passed through each machine and whether the process met the required standards. The software records this information and supplies it to the customer’s process control system on demand. The GF tool Process Inspector introduces a new dimension in traceability. It produces a digital twin of each product that accompanies the real component through all the production steps. “During the manufacturing process, both the individual production steps and the sensor data from the machines is captured and visualized,” says Sendler. “You can then automatically see when certain parameters – for instance, the internal machine temperature or the pressure in the irrigation pump – exceed tolerances.” That way, GF customers can respond immediately and correct the parameters before the machine starts producing scrap. That is what a sustainable solution looks like. Artificial intelligence (AI) will offer even more insight into the manufacturing process in the future. GF Machining Solutions is currently working on AI applications designed to autonomously improve processes and parameters. At present, people are still responsible for this step, but in five to ten years, AI may be monitoring production, predicting problems before they occur, and intervening to prevent them.
Producing perfect products faster
Intelligent solutions also play a role in the other two GF divisions. At GF Casting Solutions, for example, AI- based data evaluation is used to accelerate production processes. The division produces more than 600 different die-cast components for premium automotive manufacturers around the globe. Before a new component can enter serial production, the parameters of the manufacturing process must be fine-tuned to achieve a specific level of quality. And that is no easy task: “The machines turn out between 50% and 90% scrap on the first day, and the quality improves with each part over the next few days,” says Ilias Papadimitriou, Technical Expert Powertrain and Data Analytics in the development department of GF Casting Solutions in Schaffhausen (Switzerland). “Even on the third day, up to 40% of components may still have subtle errors.” It can take weeks – or even months – to achieve the target of less than 2% scrap through continuous process optimization. Papadimitriou firmly believes that intelligent solutions will help the division reach its quality target faster.
“It’s not easy to change a tried and tested process. So, ultimately it was a cultural pilot project, too.”
Ilias Papadimitriou, Technical Expert Powertrain and Data Analytics
Back when he worked on Formula 1 vehicles, he learned how comprehensive data analyses can drive success. Papadimitriou, who trained as a mechanical engineer, served from 2000 to 2005 as a project manager at Ferrari, where he did his part to secure the world championship title three years running for Michael Schumacher. “Back in the day, engineers would sit at computers and analyze data during the race so they could provide the driver with live tips for their racing strategy based on current readings,” recalls Papadimitriou, who joined GF in 2010. “It’s similar in production. During the production process, we receive huge quantities of data from sensors. We then evaluate that data and it’s right there for us to use for process optimization when we start up the installations.”
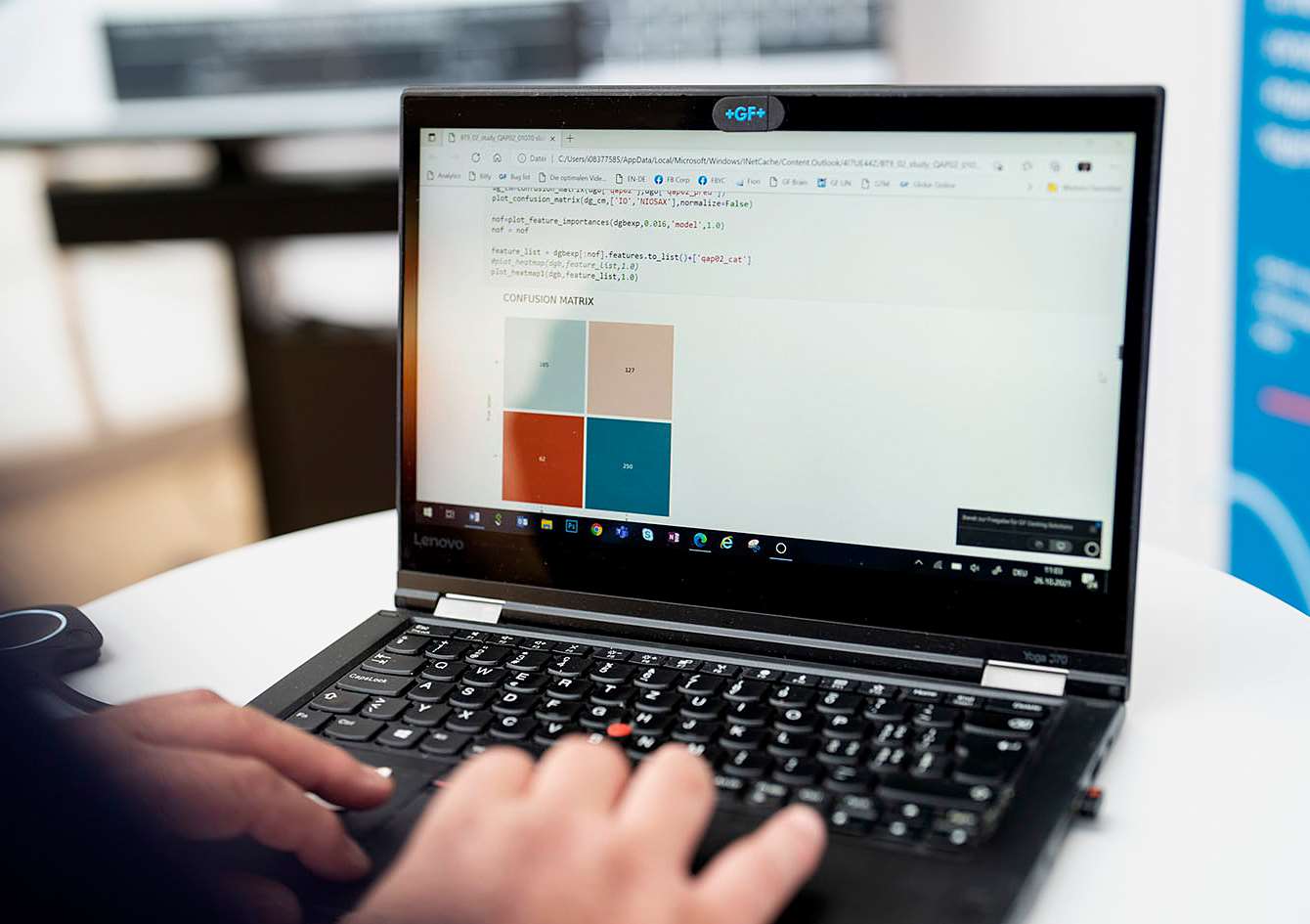
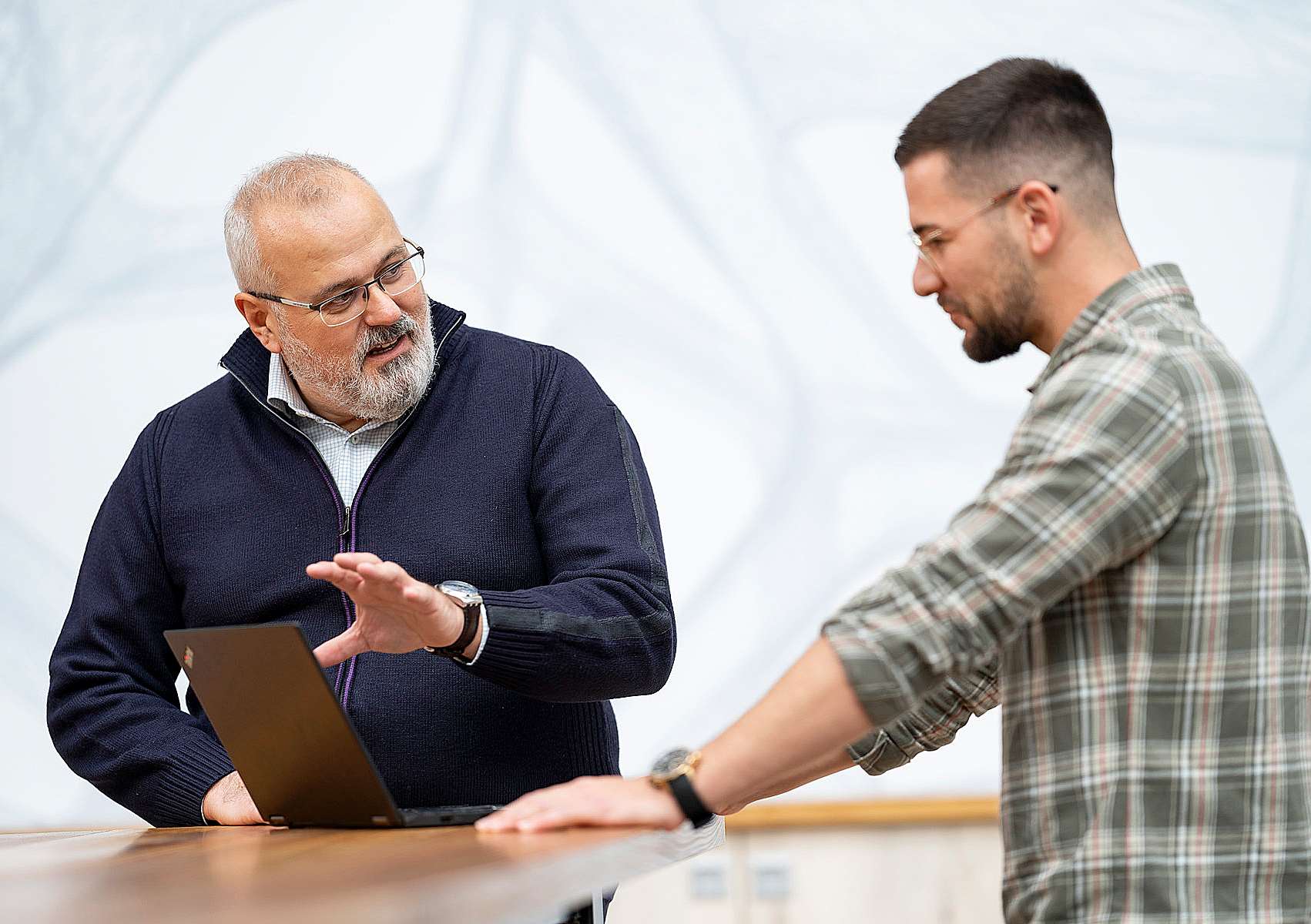
He lists a battery housing produced by GF Casting Solutions for a Renault electric vehicle as an example of this new approach. To produce this component, molten aluminum at a temperature of 600 degrees Celsius is pressed into a tool and cooled withinseconds to 200 degrees. “When we started out, many of the die-cast components were porous – meaning they had air pockets or hollow spaces – or they were warped,” says Papadimitriou. “There were around 60 independent process parameters, such as temperature or pressure in the machines, that we could tweak to improve the quality.” Up until now, this has been a laborious process, as production workers were forced to test new parameters over and over again, and inspect how each of those changes altered the quality of the product.
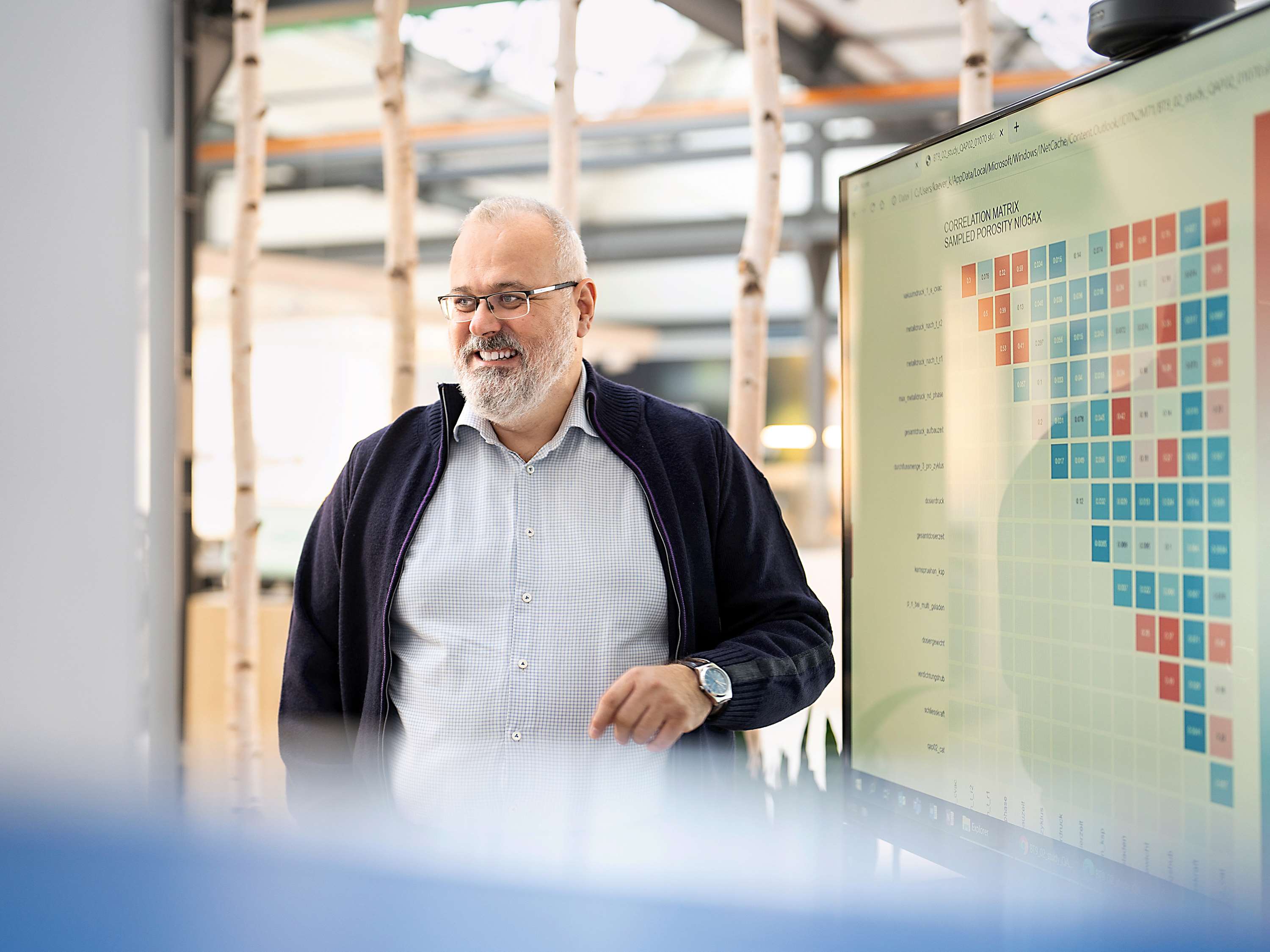
In 2019, together with the production experts from the Altenmarkt (Austria) plant and AI specialists from Microsoft, Papadimitriou developed an AI model tailored specifically for GF that would analyze sensor data during production run-up and suggest improvements to parameters such as piston force or melting point. “Using this new method, we were able to find the optimum values within just a few days and come very close to our quality target,” he says. Ultimately, the process saved the team weeks of work.
AI methods as the new standard
The pilot project is now ready for implementation in other GF Casting Solutions plants. These AI methods may soon be the new standard in the division. And that’s just the first step. In the future, Papadimitriou and his colleagues not only plan to use individual production values, they also want to analyze the way these readings change over time. “We’re interested in looking at the acceleration of the piston that presses the molten aluminum into the mold, for instance,” says Papadimitriou. “If we account for data like that, artificial intelligence can help us optimize our production process even faster and further reduce scrap.”
This represents a major advantage for GF customers. Competition is stiff, particularly in the e-mobility sector, and it is important to launch new models on the market quickly. The new AI method is sustainable, because it minimizes the demand for energy and raw materials. In addition, it optimizes production costs by reducing scrap.
“It’s not easy to change a tried and tested process, so this project was a major undertaking for the team. We were only able to succeed because we worked so closely with our colleagues from manufacturing and because they were very open to our ideas. So, ultimately it was a cultural pilot project, too,” says Papadimitriou. His advice for future innovation initiatives: “You always need to focus on the exact problem you want to solve if you plan to implement new methods like AI.”
Troubleshooting via video camera
Some intelligent solutions are the product of collaborations between GF and external partners. One such solution is the startup Visense based in Neuhausen near Schaffhausen (Switzerland), which began as an innovative project initiated by graduates of the Hasso-Plattner Institute ( Germany) and the University of St. Gallen (Switzerland) working in cooperation with the BMW Group. Visense developed software that uses video cameras to detect machine errors and enhance visual data using sensor information and AI-driven data analysis. This software is designed to help operators find errors in the production process more quickly and commission new machines faster.
The GF Piping Systems plant in Schaffhausen has been testing the Visense solution in a production cell for electric fusion sockets since September 2021. As part of this project, the start-up installed four cameras, numerous motion and vibration sensors, and laser light barriers in an automatic feeding system for winding heads.
At the beginning of the process, the winding heads are fed onto a conveyor belt by a vibratory bowl feeder. From here, they are individually fed into a robot that transfers them to yet another robot before inserting them into the injection molding machine or the tool. “The conveyor belt feed is constantly turning up errors. Some of the winding heads fall over or land at an angle, causing the system to jam or lock up,” says Manuel Reichhart, Manager Manufacturing Engineering at GF Piping Systems in Schaffhausen. “Employees are often forced to remove the obstructions manually, potentially even having to shut down the entire installation until they’ve finished.”
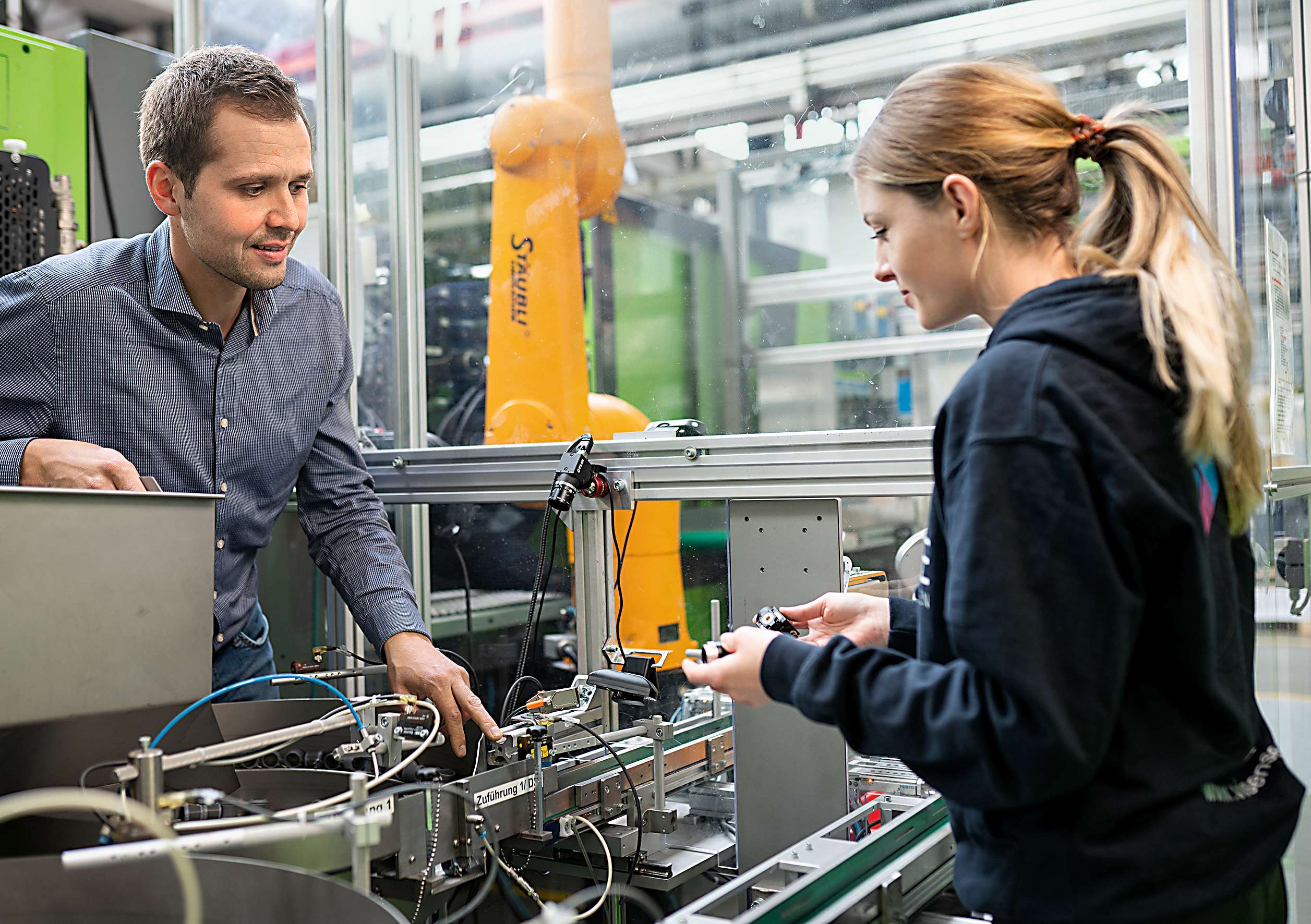
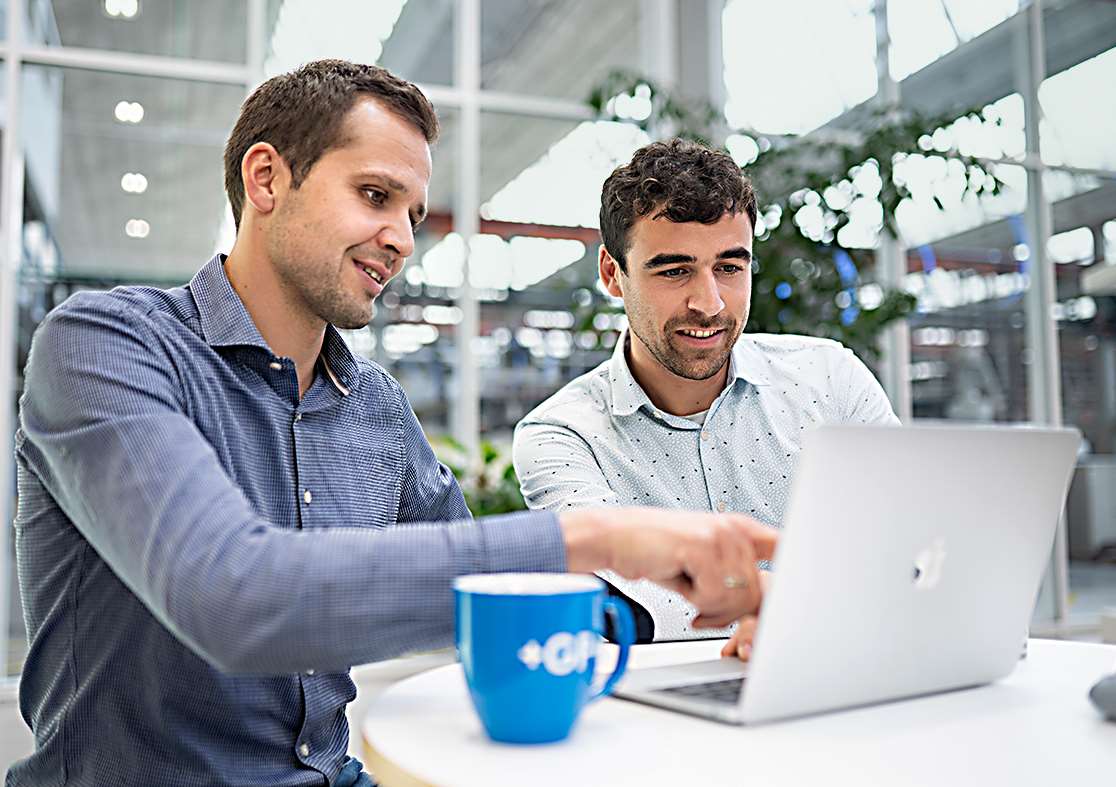
Even before the collaboration with Visense, GF had installed cameras to find the source of these errors. But this was a laborious and costly process, as employees had to manually search through the footage to filter out the relevant clips. “The Visense solution eliminates this extra work. It detects the relevant scenes and automatically assigns each incident to one of four error classes,” says Reichhart. This dramatically reduces the time it takes to pinpoint the causes of the errors. And the current Visense solution is just the beginning. The company plans to implement AI to optimize the classification of video clips and detect deviations early on in the process. This could help circumvent many errors, and preventative maintenance could completely eliminate idle times.
Learning from each other
Even though the pilot project in Schaffhausen is still in its infancy, the Visense solution is already automatically providing Reichhart and his colleagues with information about the frequency of each error. “Visense is quick to update its solutions,” says Reichhart. “For example, if we need any adjustments made to the software, we receive an update in a matter of days. We also check in with our Visense colleagues every two or three days.”
“Visense is quick to update its solutions. This dynamic response is very helpful for us.”
Manager Manufacturing Engineering
Visense also benefits from the cooperation with an established industry partner like GF: “ Every production installation is unique. This joint project helps us test the hardware configuration and optimize it as we go along,” says Visense co-founder Pia Spori. “Some questions – like the response of the sensors to certain environmental conditions – cannot be comprehensively tested in the laboratory. So projects like our cooperation with GF are vital to our evolution as a company.”
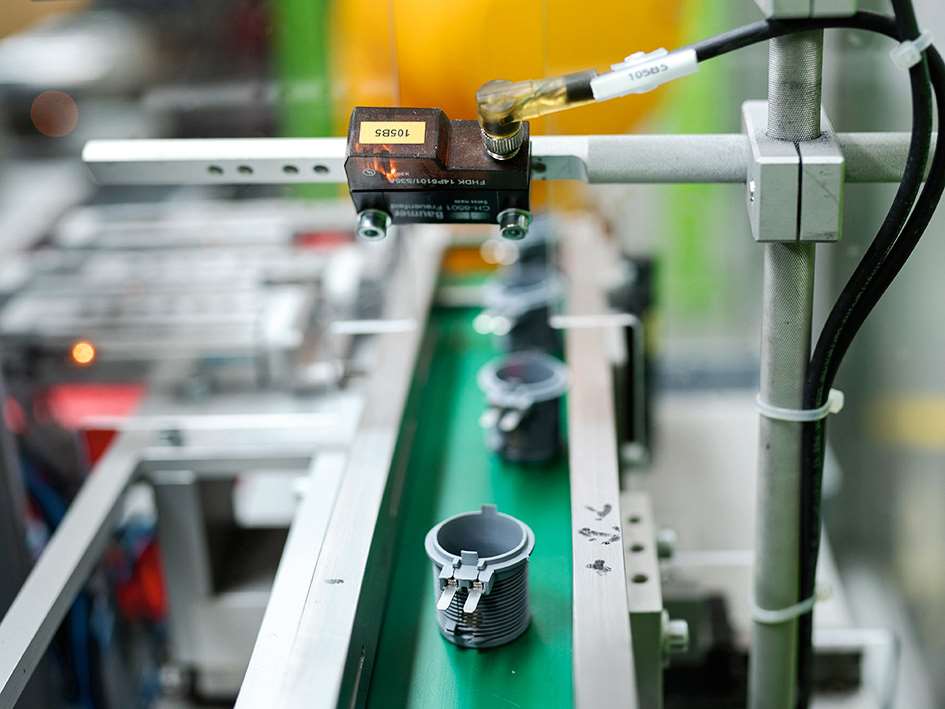
Working together on intelligent solutions to increase customer satisfaction and improve internal processes: The cooperation with Visense, the Medical Solutions Center, and the collaboration between the development center and production team at GF Casting Solutions all illustrate how work and production can each become “smarter” in their own unique ways. Thanks to the use of intelligent solutions and artificial intelligence, GF is developing ideas for the future – and that is the best way to ensure profitable growth.
Further impressions:
Read the other Spotlight articles here:
Working smarter
This is what CEO Andreas Müller has to say about the current Spotlight topic "Smart Solutions."
How we will work in 2050
Futurist Ole Wintermann has been researching how we might be working in 2050. He reveals what will change in the coming decades and how we can adapt to it.
Artificial intelligence in the workplace: blessing or curse?
What are the pros and cons of artificial intelligence (AI) and digital tools in the workplace? Employees from different regions share their answers.
A special code for GF Casting Solutions
The data matrix code is revolutionizing the production of lightweight components at GF Casting Solutions. An infographic explains how this amazing code works.