Climate pioneers
Back in 2014, System 3R in Vällingby (Sweden) was the first GF site to become carbon- neutral. This can inspire other locations to follow the same path.
Sweden is a world leader in combating climate change. For four years in a row, the country has been ranking first in the Climate Change Performance Index, which assesses the climate performances of 57 countries and the EU – accounting for over 90% of global greenhouse gas emissions.
National policies supporting the country‘s climate ambitions have already been reflected by Swedish companies for a long time and are resulting in substantial successes. System 3R, a subsidiary of GF Machining Solutions, for example, became carbon-neutral seven years ago. The company, which produces high-precision tooling and automation systems, is located in Vällingby, a borough of Stockholm, and was the first GF site to take this important sustainability step.
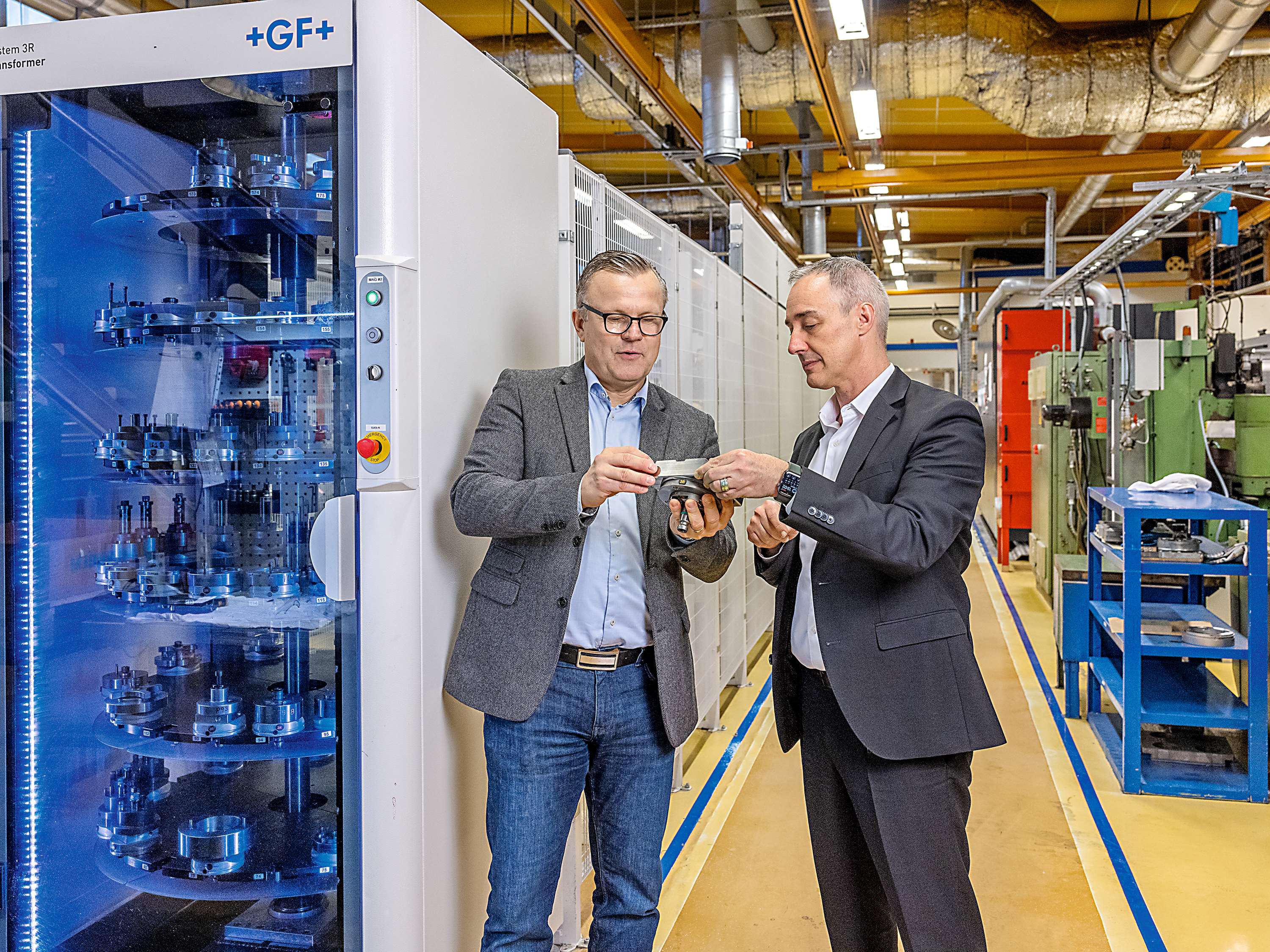
Climate protection as a part of the culture
“Being environmentally conscious is an important element of Swedish culture,” says Christophe Massart, Head of TU Tooling & Automation and Managing Director of System 3R. A native of France, Christophe has been in Sweden for less than a year but is already appreciating the eco-conscious approach to business: “The Swedes are very straightforward when it comes to enforcing environmental targets. This also applies to our GF team here in Vällingby.”
Unsurprisingly, System 3R also chose a rather straightforward path to achieving carbon-neutrality: The company opted for green electricity early on – even if this resulted in higher energy bills. Today, the company runs solely with certified energy from water power. Subsequently, it vowed to become more energy-efficient, updating all lightbulbs to LEDs and replacing all the cooling aggregates that are used to create a controlled production environment in the CMM (Coordinate Measuring Machine) rooms and grinding departments.
“Being environmentally conscious is an important element of Swedish culture.”
Christophe Massart, Head of TU Tooling & Automation and Managing Director of System 3R
This attention to the environment is also reflected in the general attitude of the employees, many of whom cycle to work – weather permitting – or use public transport or hybrid cars. Christophe himself chose the last option, opting for a Volvo, of course.
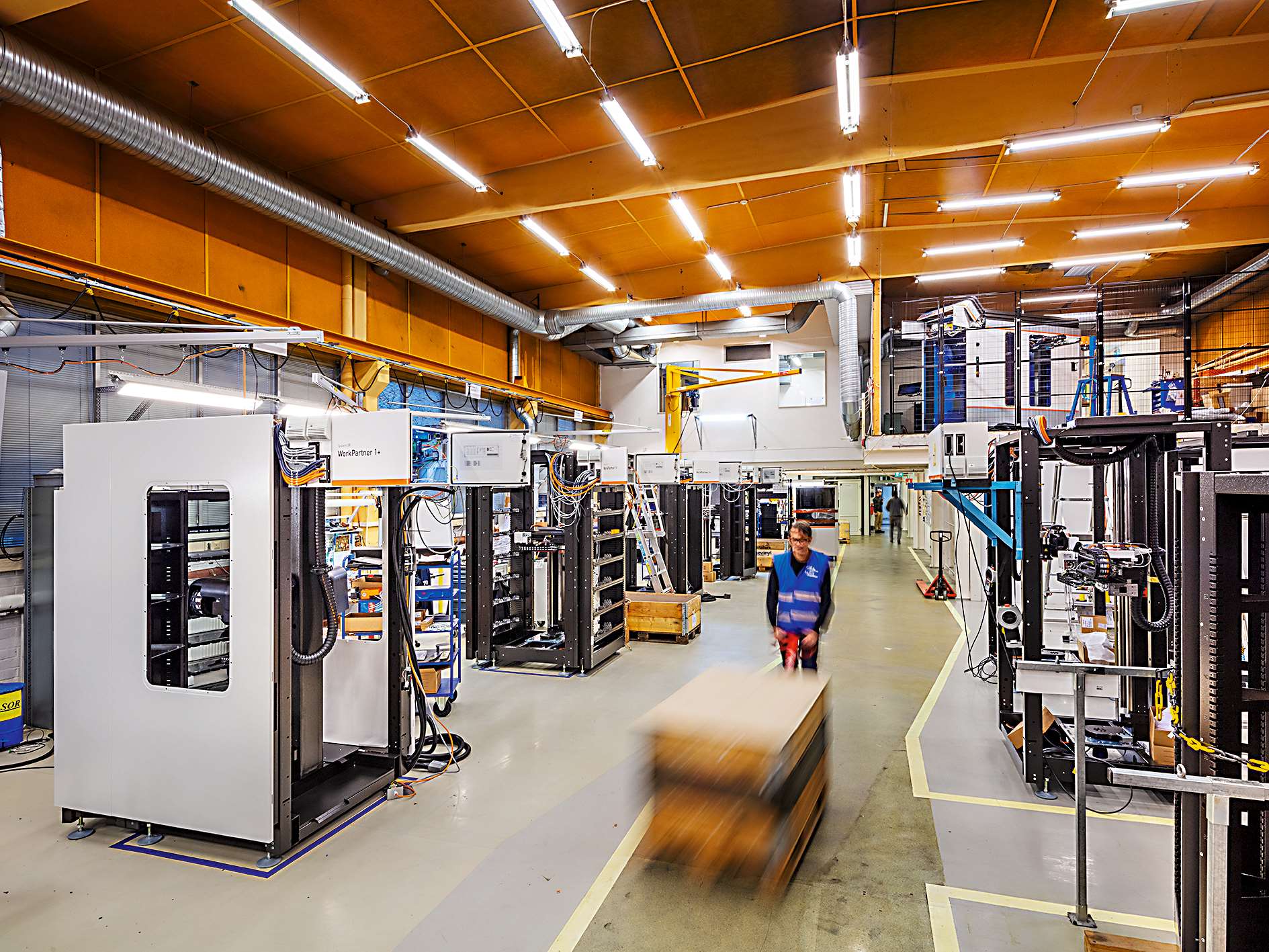
An international team
The atmosphere at System 3R is characterized by a familiar, yet international flair: 180 employees from 21 countries as far as China, Malaysia, and Tanzania work here – and many have been doing so for decades. In fact, more than one quarter of them have been with the company for more than ten years.

LEDs with a lifespan five times longer than incandescent bulbs are now in use in Vällingby.
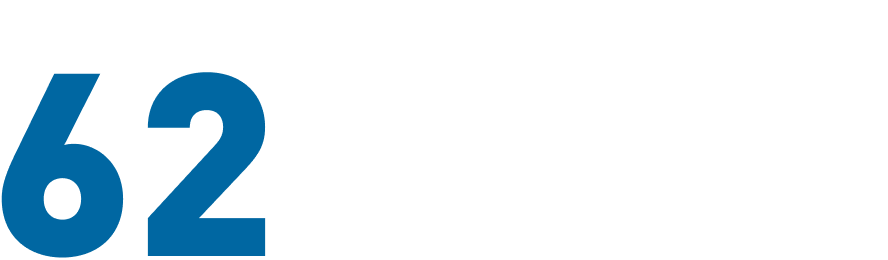
percent of the electricity generated in Sweden in 2020 came from renewable sources. Wind energy generation grew by more than one-third from 2019 to 2020.
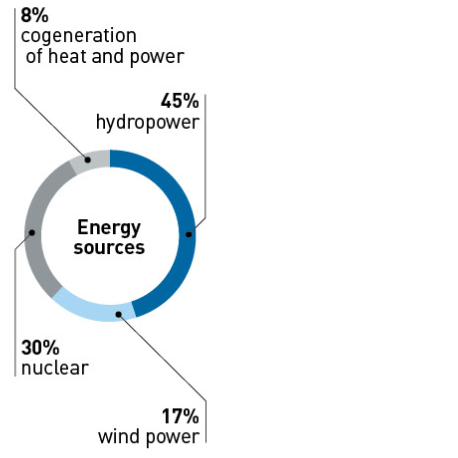
Source: Central Office of Statistics, Sweden (SCB)/ekonomifakta.se
“We want to participate proactively in achieving GF’s sustainability targets,” explains Christophe. This is done through the sale of System 3R’s high-precision tooling to the rest of GF Machining Solutions and its customers. The better and more precise the tooling, the longer it lives and the less waste it produces, creating a range of benefits: The tools have to be replaced less frequently and use less energy while in operation. “Our target is to provide customers with products that increase productivity, while being sustainable in terms of energy,” Christoph says.
Meanwhile, at System 3R the effort continues. Having reached carbon-neutrality, the company now wants to become even more energy-efficient and consume less water. One idea is to do this by prolonging the lifetime of the coolant water needed in the milling and lathe CNC machines by cleaning it from bacteria using ultraviolet light.
Given that approximately 50 tons of water are used annually at System 3R for cooling, being able to use the same water twice would lead to substantial savings. Currently, the industrial solutions for this are too expensive, but System 3R hopes cheaper ones will eventually become available – and maybe even be produced within GF.