Smart in die Zukunft
Wie GF intelligente Lösungen intelligent einsetzt und damit eigene und Kunden-Prozesse verbessert, zeigen Beispiele aus den Divisionen.
Wer das im Juli 2021 neu eröffnete Medical Solutions Center (Medical CoC – Center of Competence) von GF Machining Solutions in Schorndorf (Deutschland) besucht, mag sich im ersten Moment wie in einem exklusiven Autohaus fühlen. Statt Autos stehen dort verschiedene GF Maschinen, von Scheinwerfern illuminiert und wie edle Sportwagen präsentiert. Mit den Ausstellungsstücken lassen sich medizintechnische Produkte herstellen. „Wir können unseren Kunden hier den gesamten Herstellungsprozess erklären und vor ihren Augen sogar Prototypen fertigen“, sagt Benjamin Sendler, der in dem 1’200 Quadratmeter grossen Showroom des Medical CoC regelmässig Geschäftsführer, Produktionsexperten und Maschinenbediener empfängt. Das Medical CoC ist mit seinen innovativen Maschinen und Software-Tools für den Medizinbereich ein Beispiel für smarte Lösungen bei GF – passend zur Strategie 2025, die Wachstum durch intelligente und nachhaltige Lösungen als Ziel definiert. Wobei „intelligent“ im Fall des Medical CoC gleich mehrere Dimensionen hat: Die Kunden profitieren einerseits von intelligenten Maschinen und andererseits von der smarten Software, die die Produktion steuert und Produktionsdaten nachvollziehbar aufzeichnet. Mit beiden finden Besucher des Medical CoC die Lösung, die optimal zu ihrer individuellen Anwendung passt.
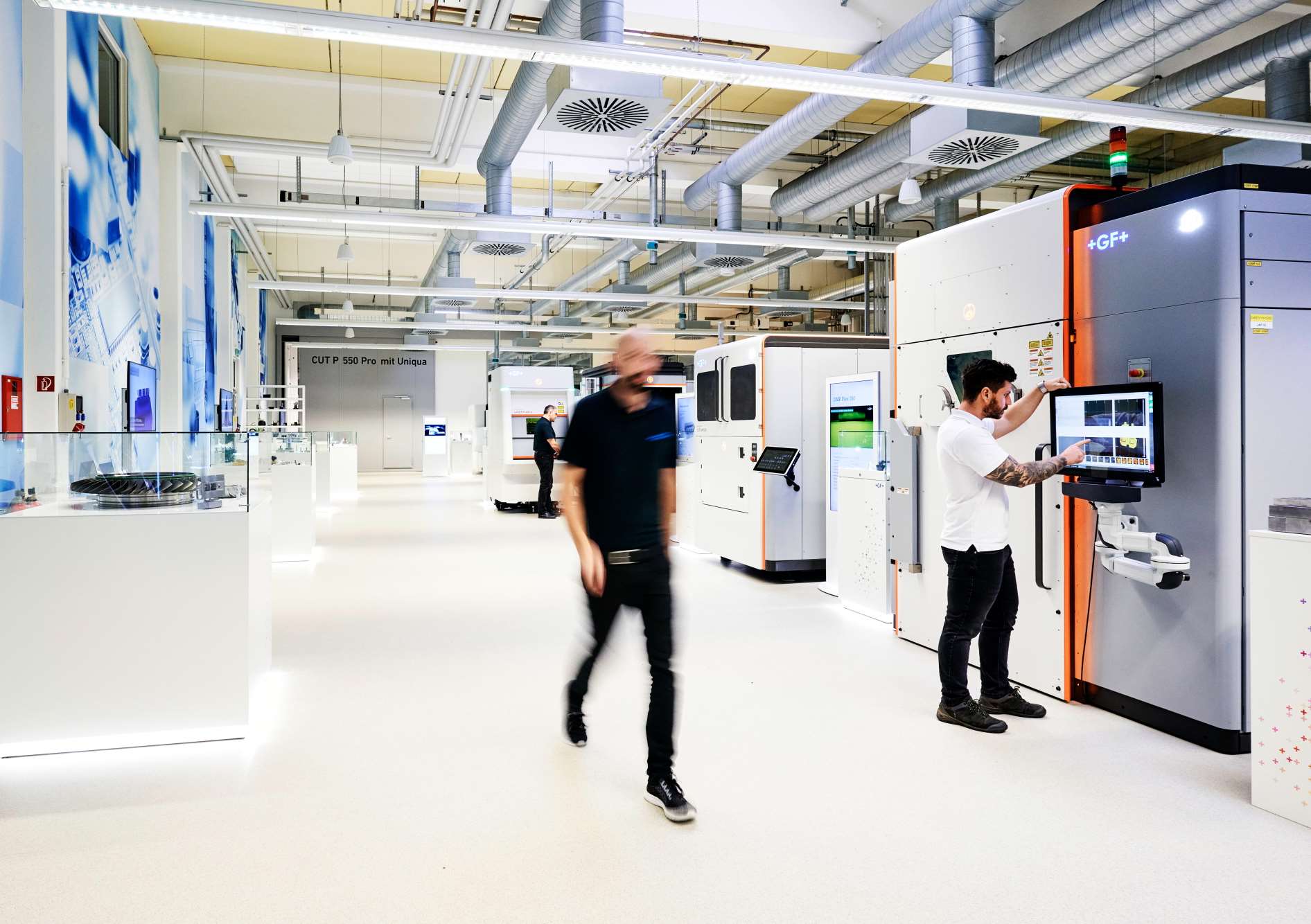
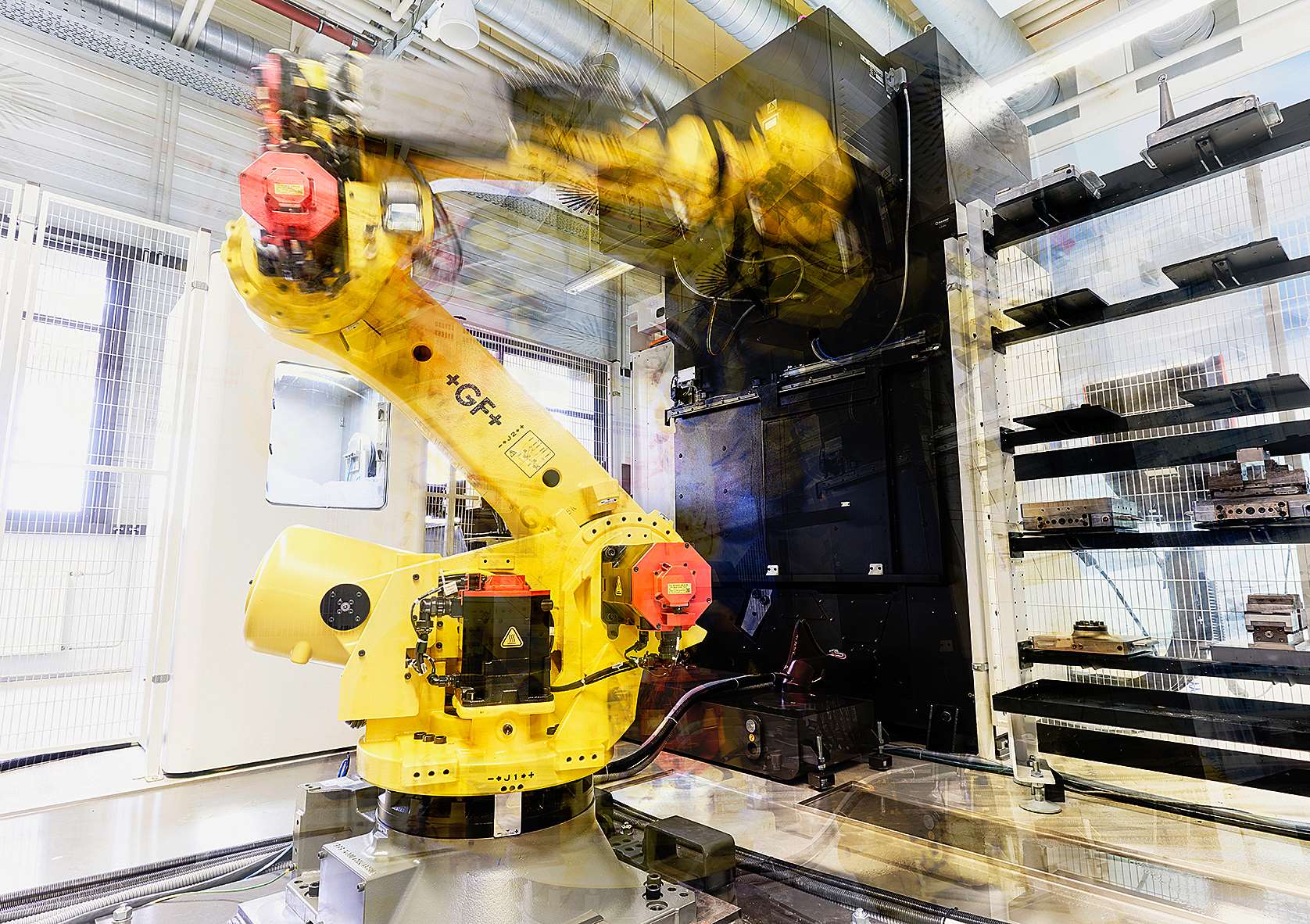
Die Herstellung hautnah miterleben
Benjamin Sendler erklärt an einem Beispiel, wie das in der Praxis aussehen kann: Für das Einsetzen von Knie-Implantaten braucht der Operateur einen sogenannten chirurgischen Schnittblock. Dieser wird an den Unterschenkelknochen (Tibia) angesetzt und legt fest, an welcher Stelle der Operateur das beschädigte Kniegelenk absägen muss. Im Medical CoC kann ein Kunde den Herstellungsprozess des chirurgischen Hilfsmittels hautnah miterleben: Der Auftrag wird in der GF Software WorkShopManager angelegt, danach durchläuft der Edelstahl-Rohling papierlos mehrere hochpräzise Fertigungsschritte – vom Fräsen über die Lasertexturierung bis hin zum Schneiden des Sägeschlitzes. „Nach diesen drei Bearbeitungsschritten liegt das fertige Bauteil vor unseren Besuchern auf dem Tisch und die Fertigungsdaten können über einen QR-Code abgerufen werden“, so Sendler. „Neben den für den Schnittblock eingesetzten Bearbeitungstechnologien stehen im Medical CoC noch weitere Lösungen zur Verfügung – zum Beispiel für die additive Fertigung von Schultergelenk-Implantaten mit ihren porösen Oberflächen. Dank des umfangreichen Portfolios lassen sich viele medizintechnische Produkte komplett mit GF Maschinen produzieren.“
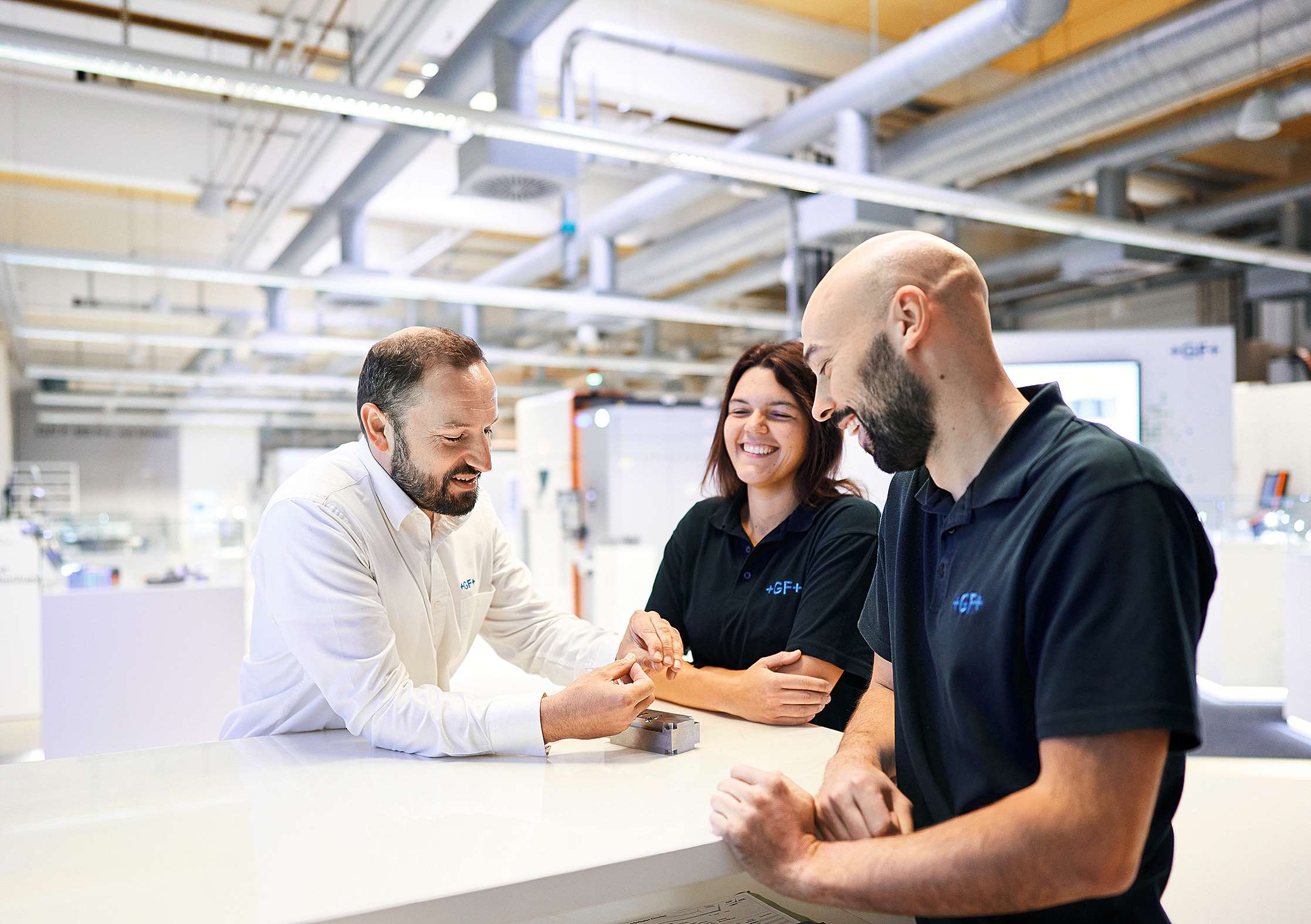
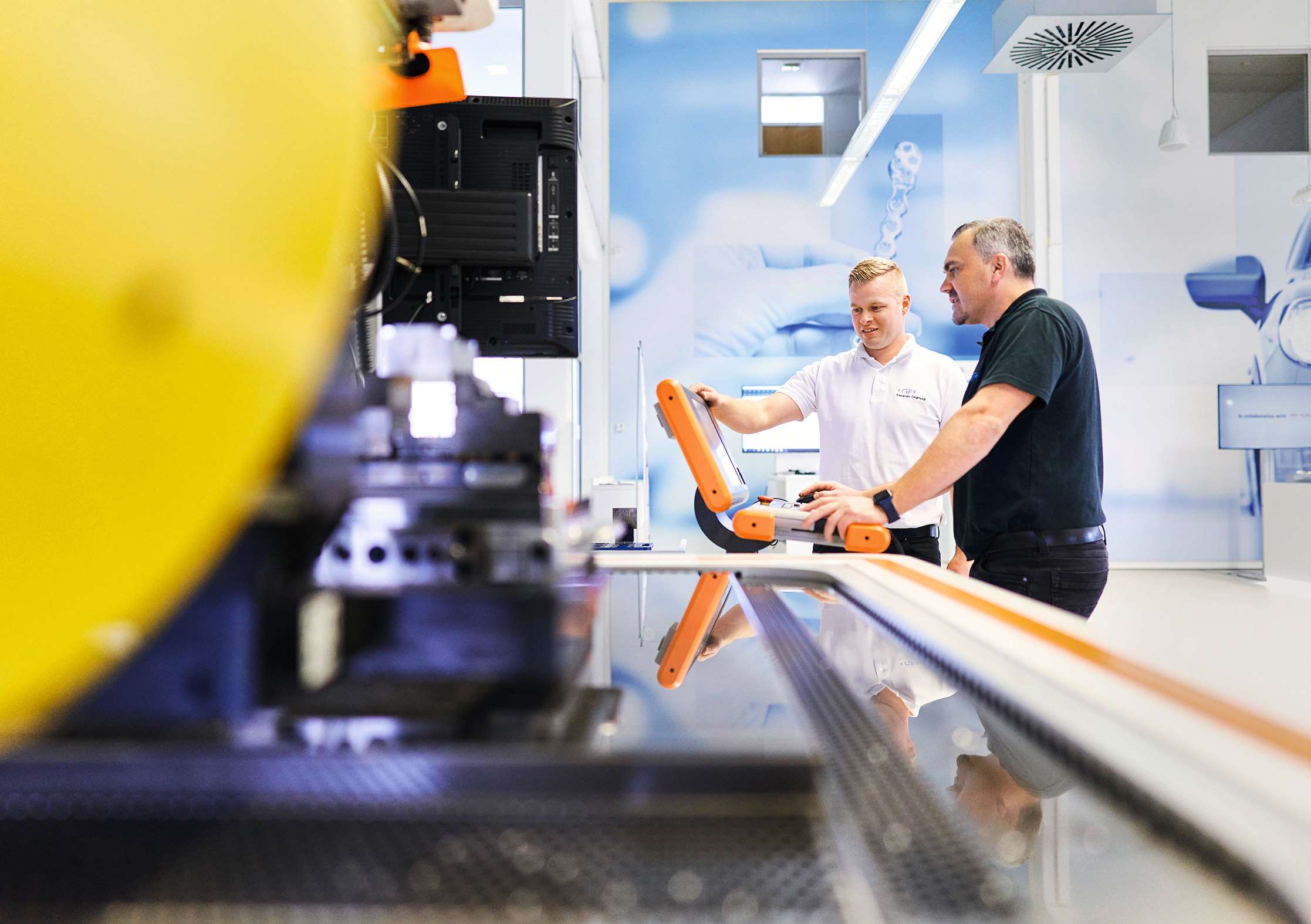
Neue Dimension der Nachverfolgbarkeit
In der Medizintechnik ist wegen der hohen gesetzlichen Anforderungen maximale Transparenz gefragt: Für bestimmte Produkte muss nachvollziehbar sein, wann es auf welcher Maschine bearbeitet wurde und ob der Prozess den Vorgaben entsprochen hat. Diese Informationen zeichnet die Software auf und liefert sie auf Wunsch an das Prozesssteuerungssystem des Kunden. Eine neue Dimension der Nachverfolgbarkeit erschliesst das GF Tool „Process Inspector“: Es erstellt einen digitalen Zwilling jedes Produktes, der das reale Bauteil durch alle Fertigungsschritte begleitet. „Neben den einzelnen Produktionsschritten werden während der Fertigung auch die Sensordaten der Maschinen aufgezeichnet und visualisiert“, erklärt Sendler. „Man erkennt dadurch sofort, wenn bestimmte Parameter aus dem Toleranzbereich herauslaufen – etwa die Temperatur in der Maschine oder der Druck einer Spülpumpe.“ So können Kunden von GF sofort eingreifen und die Parameter nachjustieren, bevor Ausschuss entsteht. Das ist eine nachhaltige Lösung. In Zukunft soll Künstliche Intelligenz (KI) noch mehr Einsichten in den Herstellungsprozess liefern. GF Machining Solutions arbeitet an KI-Anwendungen, die Prozesse und Parameter selbstständig verbessern können. Während heute noch Menschen dafür zuständig sind, könnte in fünf bis zehn Jahren KI die Fertigung überwachen, Probleme vorhersehen und rechtzeitig eingreifen.
Schneller zum fehlerfreien Produkt
Auch in den anderen beiden GF Divisionen kommen intelligente Lösungen zum Einsatz: Zum Beispiel bei GF Casting Solutions, wo KI-basierte Datenauswertung den Produktionsanlauf beschleunigt. Die Division produziert mehr als 600 verschiedene Druckgussteile für Premium-Automobilhersteller weltweit. Bevor eine neue Komponente in Serienproduktion geht, müssen die Parameter des Herstellungsprozesses eingestellt werden, um ein bestimmtes Qualitätsniveau zu erreichen. Das ist keine einfache Aufgabe: „Am ersten Tag wird oft zwischen 50 und 90 Prozent Ausschuss produziert, im Lauf der folgenden Tage verbessert sich die Qualität dann Stück für Stück“, berichtet Ilias Papadimitriou, der in der Entwicklungsabteilung von GF Casting Solutions in Schaffhausen (Schweiz) als Technical Expert Powertrain und Data Analytics arbeitet. „Auch am dritten Tag sind bis zu 40 Prozent der Komponenten oft noch nicht ganz fehlerfrei.“ Bis dieser Wert durch kontinuierliche Optimierung der Prozesse bei den angestrebten weniger als zwei Prozent Ausschuss liegt, vergehen oft Wochen, manchmal sogar Monate. Für Papadimitriou steht fest: Intelligente Lösungen können dabei helfen, schneller das Qualitätsziel zu erreichen.
„Es ist nicht einfach, bewährte Prozesse zu verändern. Unser Projekt war so gesehen auch ein kulturelles Pilotprojekt.“
Ilias Papadimitriou, Technical Expert Powertrain und Data Analytics
Während seiner Zeit in der Formel 1 hat Papadimitriou gelernt, wie umfangreiche Datenanalysen zum Erfolg führen. Der Maschinenbauingenieur war von 2000 bis 2005 Projektleiter bei Ferrari und trug seinen Teil dazu bei, dass Michael Schumacher dreimal in Folge Weltmeister wurde. „Damals sassen die Ingenieure an Bildschirmen und haben während des Rennens Daten ausgewertet, um dem Fahrer auf Basis der aktuellen Messwerte live Anweisungen für die Rennstrategie geben zu können“, erinnert sich Papadimitriou, der seit 2010 bei GF arbeitet. „In der Produktion ist das ganz ähnlich: Auch dort erhalten wir während des Produktionsprozesses zahlreiche Daten von Sensoren, die wir auswerten und beim Hochfahren der Anlagen sofort für die Prozessoptimierung nutzen könnten.“
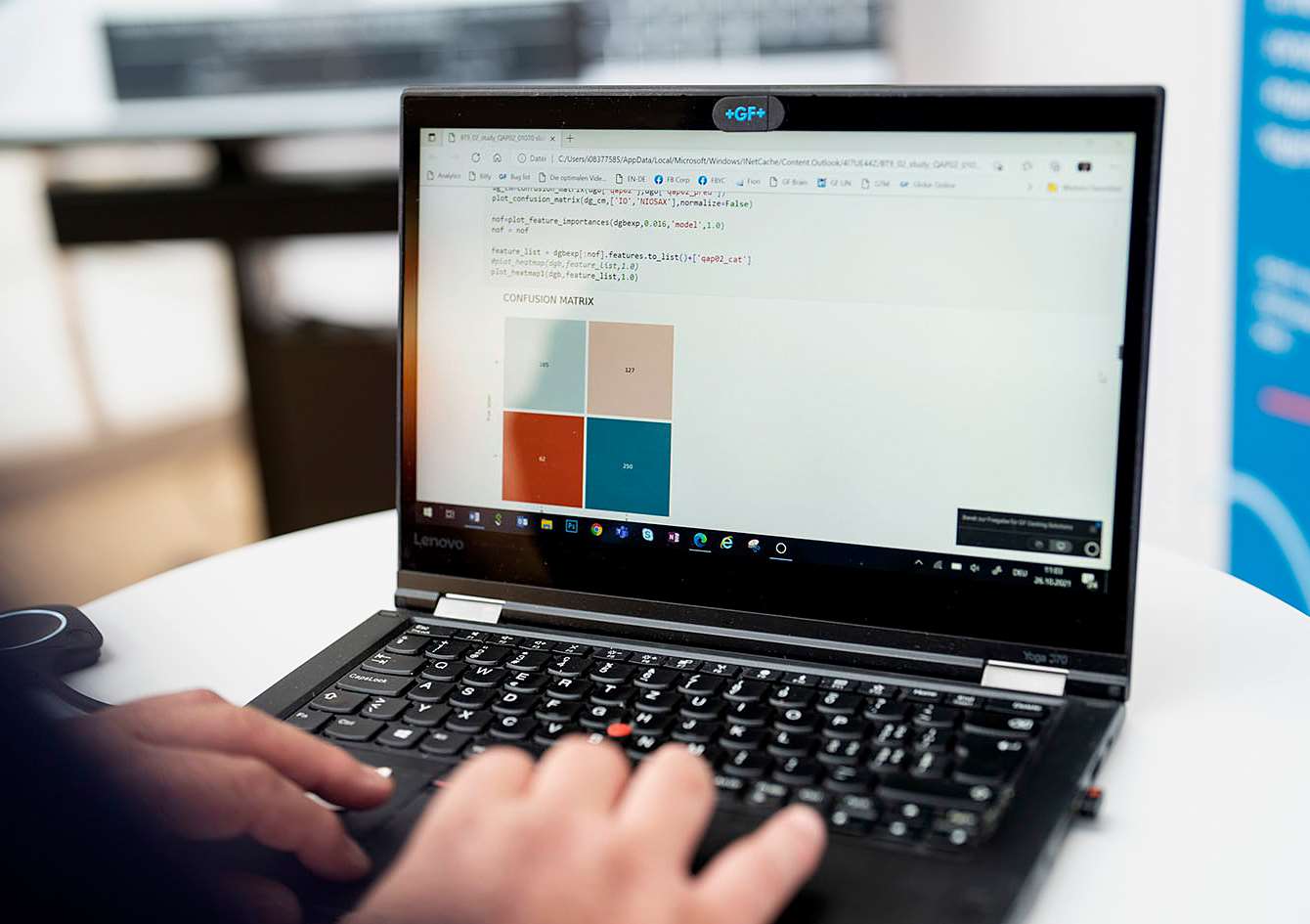
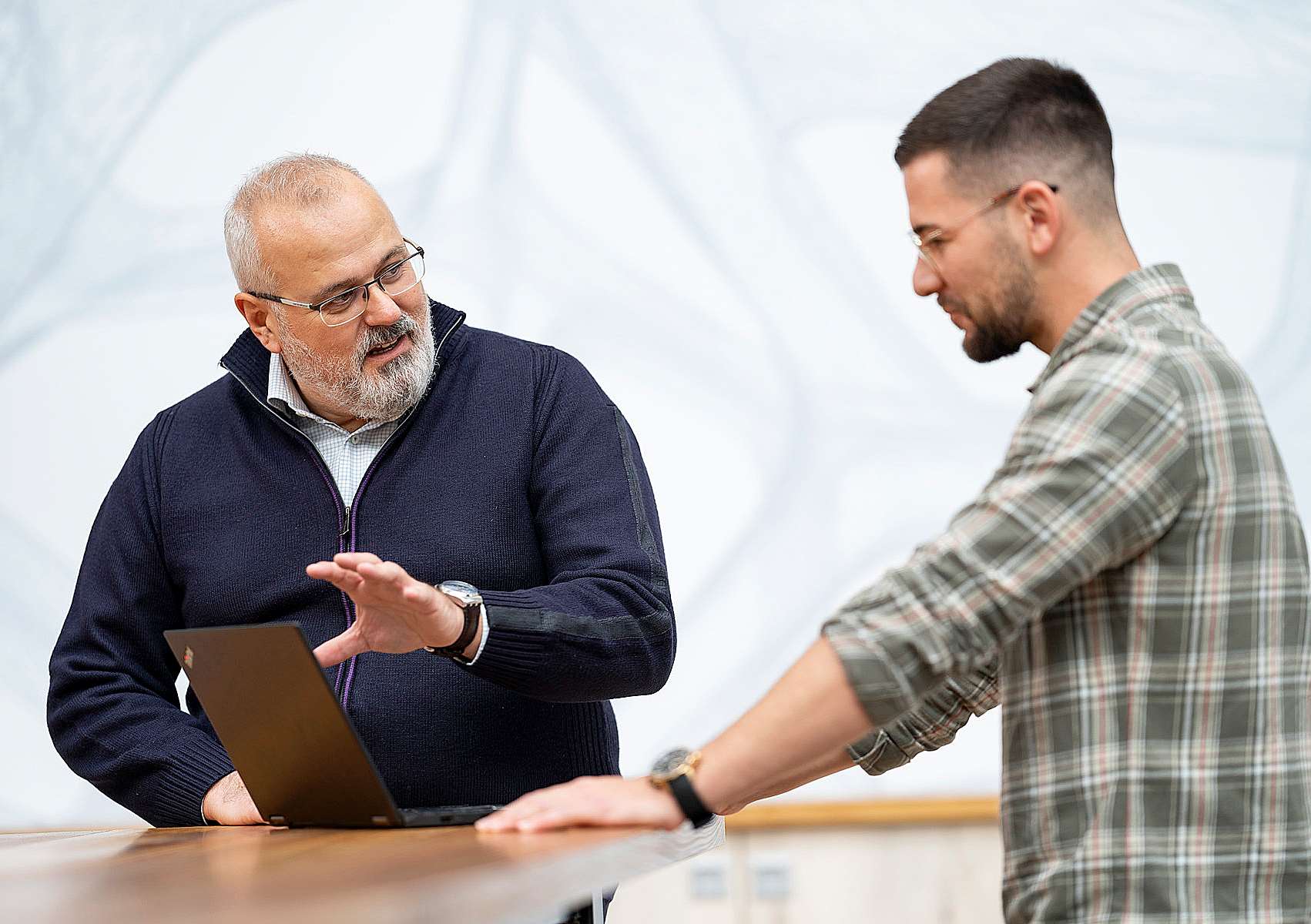
Als Beispiel für den neuen Ansatz nennt Papadimitriou ein Batteriegehäuse, das GF Casting Solutions für ein Elektrofahrzeug von Renault produziert. Dafür wird geschmolzenes Aluminium bei 600 Grad Celsius in ein Werkzeug gepresst und danach innerhalb weniger Sekunden auf 200 Grad abgekühlt. „Anfangs hatten viele der Druckguss-Teile Porositäten, das heisst Lufteinschlüsse oder Hohlräume, oder waren verzogen“, berichtet Papadimitriou. „Um ihre Qualität zu verbessern, können wir rund 60 unabhängige Prozessparameter wie die Temperatur oder den Druck in den Maschinen variieren.“ Bisher war das ein langwieriger Prozess, denn die Produktionsmitarbeiter mussten immer wieder neue Parameterwerte testen und dann deren Auswirkungen auf die Produktqualität überprüfen.
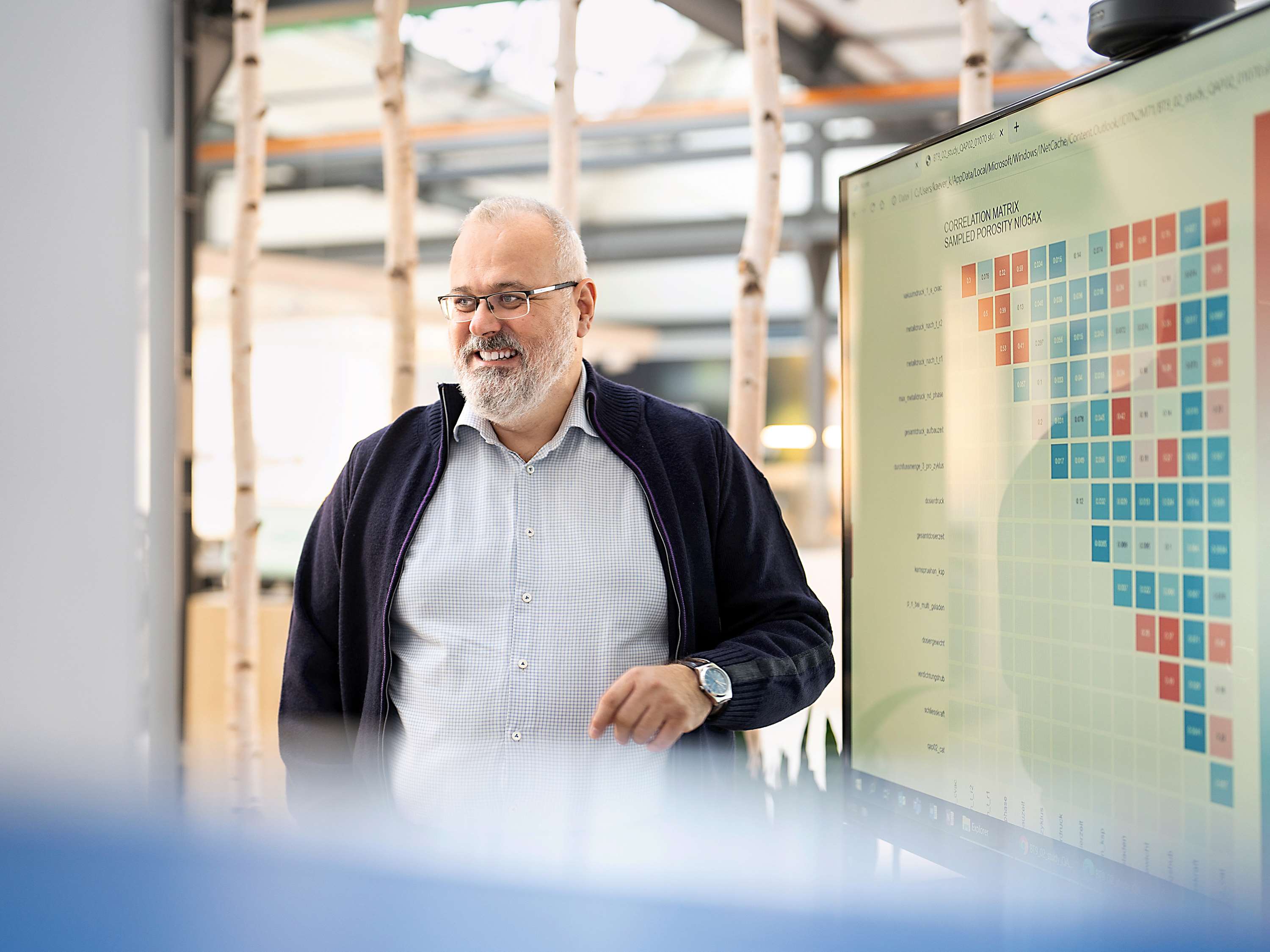
Gemeinsam mit den Produktionsexperten aus dem Werk Altenmarkt (Österreich) und KI-Spezialisten von Microsoft entwickelte Papadimitriou 2019 ein individuell auf GF zugeschnittenes KI-Modell, das während des Produktionshochlaufs Sensordaten analysiert und Verbesserungen der Parameter vorschlägt – zum Beispiel für den Kolbendruck oder die Schmelztemperatur. „Mit der neuen Methode hatten wir bereits nach einigen Tagen die optimalen Werte gefunden und sind so unserem Qualitätsziel schon sehr nahe gekommen“ – eine Zeitersparnis von mehreren Wochen.
KI-Methode als neuer Standard
Mittlerweile ist das Pilotprojekt bereit für die Einführung in anderen Werken von GF Casting Solutions. Bald könnte die KI-Methode ein neuer Standard in der Division werden. Und dabei soll es nicht bleiben: Papadimitriou und seine Kollegen wollen in Zukunft nicht nur einzelne Messwerte aus der Produktion nutzen, sondern auch deren zeitliche Verläufe. „Uns interessiert zum Beispiel, mit welcher Beschleunigung der Kolben das geschmolzene Aluminium in die Form presst“, so Papadimitriou. „Wenn wir auch solche Daten miteinbeziehen, kann uns die Künstliche Intelligenz dabei unterstützen, unsere Produktionsprozesse noch schneller zu optimieren und den Ausschuss weiter zu reduzieren.“
Für Kunden von GF ist das ein entscheidender Vorteil, denn gerade bei der E-Mobilität ist der Wettbewerb gross und eine schnelle Markteinführung neuer Modelle wichtig. Die neue KI-Methode ist nachhaltig, weil sie den Einsatz von Energie und Rohstoffen verringert. Ausserdem werden durch die Reduktion des Ausschusses die Produktionskosten optimiert.
„Es ist nicht einfach, bewährte Prozesse zu verändern, deshalb war das Projekt eine grosse Teamleistung. Sie war nur möglich, weil wir eng mit den Kolleginnen und Kollegen aus der Fertigung zusammengearbeitet haben und sie sehr offen für unsere Ideen waren. So gesehen war es auch ein kulturelles Pilotprojekt,“ sagt Papadimitriou. Sein Rat für andere Innovationsvorhaben: „Man sollte sich unbedingt auf ein konkretes Problem fokussieren, das man lösen möchte, wenn man neue Methoden wie KI implementieren möchte.“
Fehlerjagd per Videokamera
Einige intelligente Lösungen entstehen bei GF auch gemeinsam mit externen Partnern. Einer davon ist das Start-up Visense aus Neuhausen nahe Schaffhausen, das aus einem Innovationsprojekt von Absolventen des Hasso-Plattner- Instituts (Deutschland) und der Universität St. Gallen (Schweiz) in Zusammenarbeit mit der BMW Group hervorgegangen ist. Visense hat eine Software entwickelt, die Maschinenfehler mit Videokameras erfasst und die visuellen Daten durch Sensorinformationen und eine KI-gesteuerte Datenanalyse anreichert. So sollen sich Fehler in Produktionsprozessen schneller finden und neue Maschinen schneller hochfahren lassen.
Das Schaffhauser Werk von GF Piping Systems testet die Visense-Lösung seit September 2021 in einer Fertigungszelle für Elektroschweissmuffen. Dafür hat das Start-up neben vier Kameras auch Bewegungs- und Vibrationssensoren sowie Laser-Lichtschranken in ein automatisches Zuführsystem für Wicklungsträger eingebaut.
Zu Beginn des Prozesses werden die Wicklungsträger von einem Vibrationswendelförder über ein Förderband mit Vereinzelung einem Roboter zugeführt, der sie einem weiteren Roboter übergibt, bevor sie in die Spritzgussmaschine beziehungsweise in das Werkzeug eingelegt werden. „Bei der Zuführung über das Band kommt es immer wieder zu Störungen: Manche Wicklungsträger fallen zum Beispiel um oder verkanten, sodass auf dem Zuführungsband ein Stau beziehungsweise eine Verklemmung entsteht“, erklärt Manuel Reichhart, Leiter Betriebsmittelplanung bei GF Piping Systems in Schaffhausen. „Oft muss dann ein Mitarbeitender die Störung von Hand beheben. So lange steht möglicherweise die gesamte Anlage.“
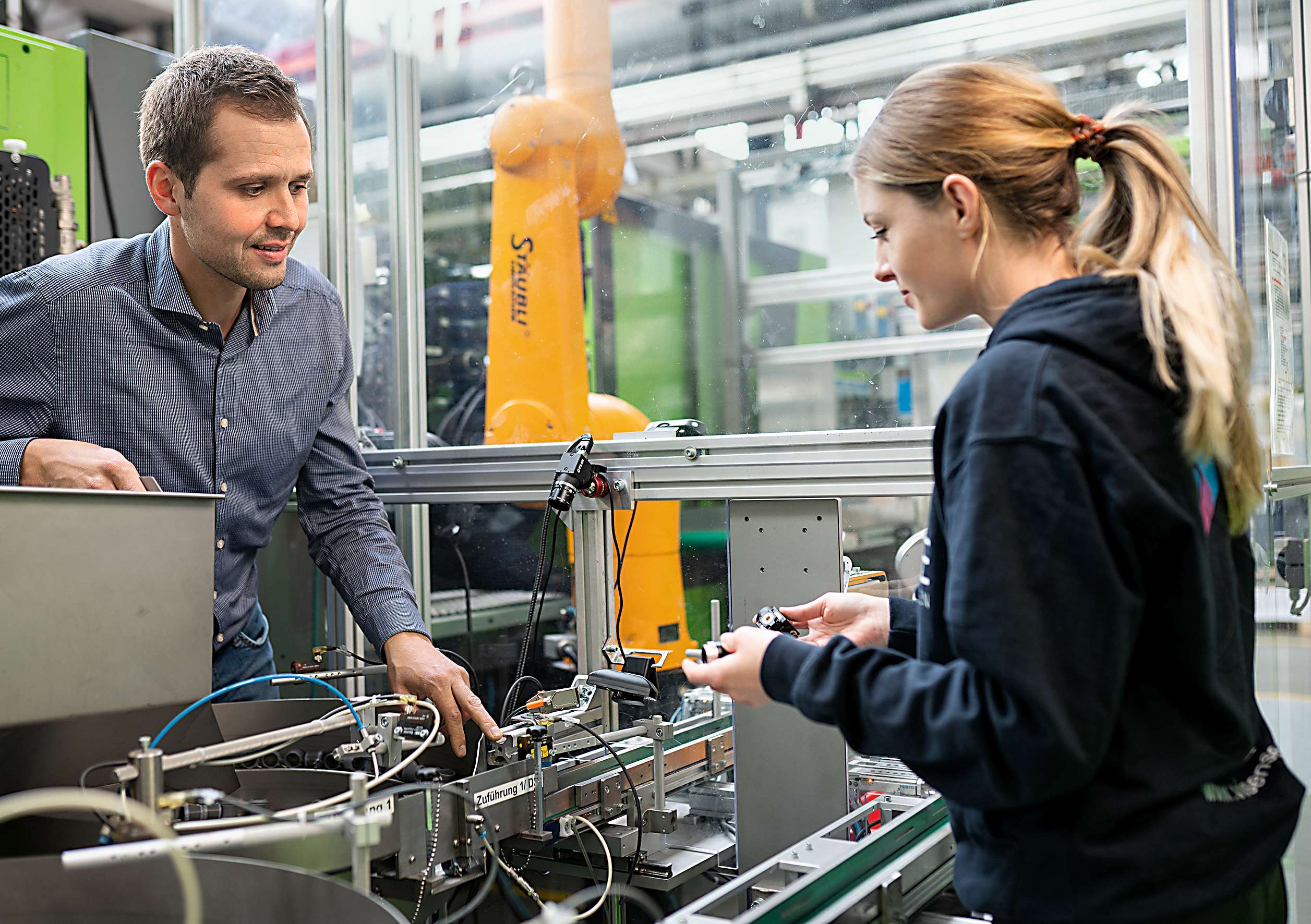
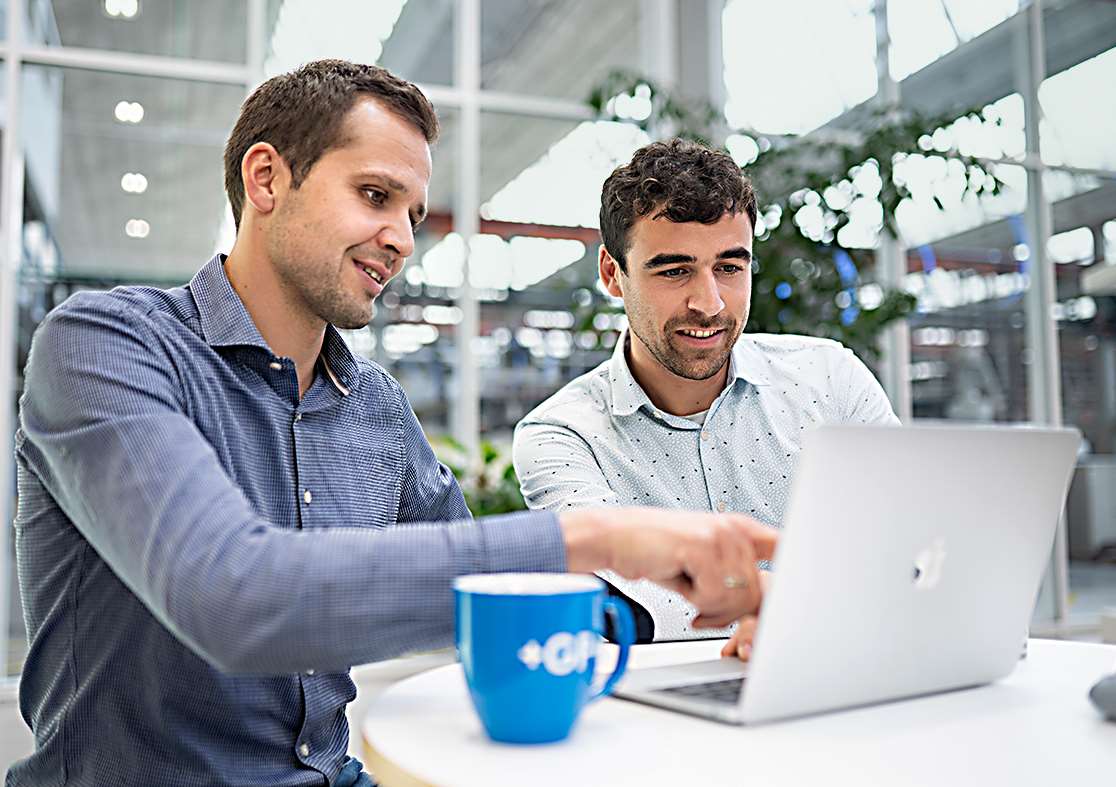
Schon vor der Zusammenarbeit mit Visense suchten bei GF Kameras nach den Ursachen für solche Fehler. Das war allerdings mit hohem Aufwand verbunden, weil Mitarbeitende aus den Videoaufnahmen von Hand die entscheidenden Passagen herausfiltern mussten. „Die Visense-Lösung nimmt uns diese Arbeit ab: Sie erkennt die relevanten Szenen und ordnet sie automatisch jeweils einer von vier Fehlerklassen zu“, so Reichhart. Das verringert den Aufwand für die Ursachenforschung deutlich. Die aktuelle Visense-Lösung ist erst der Anfang. Das Unternehmen plant, in Zukunft auch KI einzusetzen, um die Zuordnung der Videoclips zu optimieren und Abweichungen im Prozess noch früher zu erkennen. So liessen sich viele Fehler und ein Anlagenstillstand möglicherweise durch vorausschauende Wartung ganz vermeiden.
Voneinander lernen
Obwohl das Pilotprojekt in Schaffhausen ganz am Anfang steht, liefert die Visense-Lösung Reichhart und seinen Kollegen bereits jetzt automatisch Informationen über die Häufigkeit der einzelnen Fehler. „Visense setzt Neuerungen schnell um“, so Reichhart. „Wenn wir beispielsweise Anpassungen an der Software für das Projekt benötigen, erhalten wir innerhalb von Tagen ein Update. Ausserdem tauschen wir uns mit unseren Visense-Kollegen alle zwei bis drei Tage aus.“
„Visense ist äusserst agil und setzt Neuerungen schnell um. Diese hohe Dynamik hilft uns sehr.“
Manuel Reichhart, Leiter Betriebsmittelplanung
Auch Visense profitiert von der Kooperation mit einem etablierten Industrieunternehmen wie GF: „Jede Produktionsanlage ist einzigartig. Das gemeinsame Projekt hilft uns, die Zusammenstellung der Hardware zu testen und weiter zu optimieren“, sagt Visense-Mitgründerin Pia Spori. „Manche Fragen wie die Reaktion der Sensoren auf die Umgebungskonditionen lassen sich im Labor nur bedingt beantworten. Darum sind Projekte wie das mit GF wichtig für unsere Weiterentwicklung.“
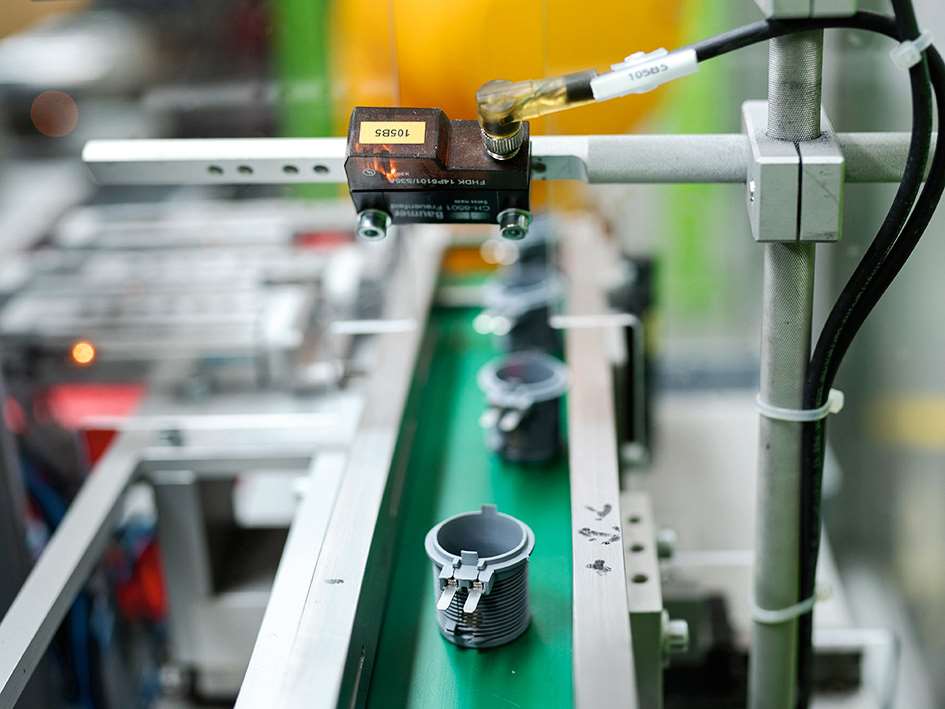
Gemeinsam an intelligenten Lösungen arbeiten, um die Zufriedenheit der Kunden zu erhöhen und interne Prozesse zu verbessern: Die Kooperation mit Visense, aber auch das Medical Solutions Center und die Zusammenarbeit von Entwicklungszentrum und Produktion bei GF Casting Solutions, zeigen, wie Arbeit und Produktion auf ganz unterschiedliche Weise noch „smarter“ werden können. Durch den Einsatz von intelligenten Lösungen und auch Künstlicher Intelligenz entwickelt GF Ideen für die Zukunft – die beste Voraussetzung für profitables Wachstum.
Weitere Impressionen:
Lesen Sie hier die weiteren Spotlight-Artikel:
Intelligentes Arbeiten
Das sagt CEO Andreas Müller zum aktuellen Spotlight-Thema "Smart Solutions".
Wie wir 2050 arbeiten
Zukunftsforscher Dr. Ole Wintermann hat erforscht, wie Arbeit im Jahr 2050 aussehen könnte. Er verrät, was sich in den nächsten Jahrzehnten ändern wird und wie wir uns darauf einstellen können.
Künstliche Intelligenz am Arbeitsplatz: Fluch oder Segen?
Welche Vor- und Nachteile bringen Künstliche Intelligenz (KI) und digitale Tools am Arbeitsplatz? Diese Frage haben Mitarbeitende aus verschiedenen Regionen beantwortet.
Ein Wundercode für GF Casting Solutions
Der Data Matrix Code revolutioniert bei GF Casting Solutions die Produktion von Leichtbaukomponenten. Wie der Wundercode funktioniert, zeigt eine Infografik.